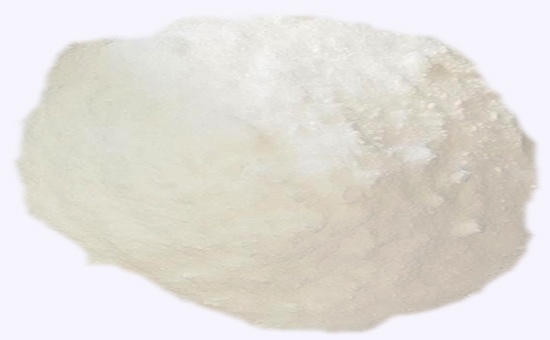
White carbon black is a non-combustible, odorless and odorless white powder with excellent high temperature resistance and electrical insulation properties. It is a light color filler with excellent reinforcing performance. It can significantly improve the tear resistance of products in the production of EPDM rubber products. Cracking performance, adhesion strength, wet skid resistance and abrasion resistance; however, when white carbon black is used as the main reinforcing agent for EPDM rubber products, improper use and unreasonable combination will directly affect the vulcanization properties of the product. Why, how to solve it?
In the sulfur vulcanization system, most of the vulcanization accelerators contain an amino group. The adsorption of white carbon black and the reaction with the accelerator will reduce the promoting dose of the vulcanization reaction in the vulcanization system of the EPDM vulcanized product; the white carbon black is acidic. The acid promoter in the vulcanization system cannot be activated; at the same time, the white carbon black reacts with the activated sulfide zinc ion to reduce the concentration of zinc ions in the rubber compound; in the sulfur vulcanization system, the white carbon black directly affects the EPDM rubber. The vulcanization rate and degree of vulcanization of the product, the higher the activity of the white carbon black on the vulcanization process. In the peroxide vulcanization system, the white carbon black not only reduces the crosslinking speed of the peroxide, but also causes the DCP vulcanized rubber to emit an unpleasant odor when it is vulcanized.
Therefore, when adding white carbon black to the EPDM rubber product, the following problems should be paid attention to to reduce the influence of silica on the vulcanization process of EPDM rubber.
ENB (ethylidene norbornene) is a third monomer introduced in EPDM rubber obtained by copolymerization of ethylene and propylene, which can improve the vulcanization rate, tensile strength and permanent compression deformation of the rubber compound. The higher the ENB content, the smaller the impact of the EPDM vulcanization is affected by the white carbon black; the reasonable control of the amount of white carbon black (30-60 parts is suitable), as far as possible to meet the reinforcement performance of the EPDM rubber products The amount of white carbon black; combined with a certain amount of furnace carbon black, magnesium oxide and other alkaline complexing agents to neutralize the acidity of silica, improve the vulcanization properties of EPDM rubber; in the sulfur vulcanization system can increase the amount of zinc oxide Or add a small amount of magnesium oxide to reduce the tendency of white carbon black to take zinc ions from the vulcanization system; increase the amount of peroxide in the peroxide vulcanization system, use 1-3 parts of co-crosslinking agent; Ethylene-propylene rubber vulcanization time.
When using EPDM reclaimed rubber to replace EPDM rubber products in whole or in part to replace EPDM rubber, the usage and dosage of silica can be referred to this article; EPDM reclaimed rubber has low price and good performance, and reasonable use of white in formula Carbon black can not only reduce the production cost of EPDM rubber products, but also improve the vulcanization properties of rubber compounds and comprehensive indicators of rubber products.
Exclusive original article [commercial authorization] reprint, excerpt and excerpt in any form are prohibited without written authorization. Focus on Hongyun rubber: learn the process formula and raw material technology of producing rubber products from recycled rubber to help you reduce costs and increase profits