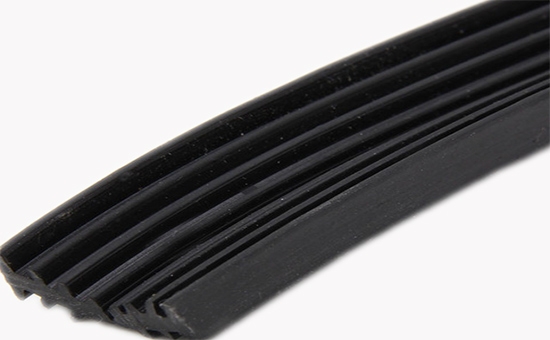
EPDM rubber has excellent heat resistance, ozone resistance, and weather resistance, and is widely used in automotive parts, waterproof materials, cable sheaths, hoses, tapes, seals and other fields. In actual production, the combined use of EPDM rubber and epdm reclaimed rubber has good vulcanization performance; however, when EPDM rubber is used in combination with other types of rubber such as natural rubber, styrene butadiene rubber, butyl rubber, etc., due to the Ethylene-propylene vulcanization speed is very slow, and it is necessary to select a suitable vulcanization system to achieve co-vulcanization.
1. Why does the combined glue need to achieve co-vulcanization?
The so-called co-vulcanization can be divided into two aspects: on the one hand, it means that the two rubber phases have almost the same vulcanization speed; on the other hand, it refers to the co-crosslinking at the interface of the two rubber phases. The rubber vulcanizing agent and accelerator 2YLYY72 have different solubility in different types of rubber, so the distribution coefficient of the vulcanizing agent in the combined rubber is different, and the vulcanization performance is different. In actual production, whether EPDM and other rubbers can achieve co-vulcanization directly affects the mechanical strength of the combined rubber.
2. The meaning of EPDM and other rubbers
EPDM rubber can be used together with natural rubber, styrene butadiene rubber or butadiene rubber and other diene rubbers. The vulcanized rubber has good physical and mechanical properties. EPDM rubber can also be used together with neoprene, nitrile rubber, butyl rubber or chlorosulfonated polyethylene. The vulcanized rubber has good comprehensive properties. Common application examples: using a certain amount of butyl rubber or butyl reclaimed rubber in EPDM sealing strips can delay the aging, hardening and brittleness of EPDM sealing strips, loss of sealing effect, and longer service life.
3. Different EPDMs are used together to achieve co-vulcanization
When EPDM is used in combination with other rubbers, it is necessary to select a suitable vulcanization system and process to achieve co-vulcanization.
In actual production, when EPDM and butyl reclaimed rubber are used together, it is recommended to use EPDM combined with DCP and butyl reclaimed rubber with sulfur/accelerator. The masterbatch blending can obtain a good vulcanization effect. When EPDM rubber and styrene butadiene rubber/natural rubber are used together, the combined vulcanization system using DCP (sulfur/accelerator) is better than pure sulfur/accelerator system. NBR/EPDM or SBR/EPDM combined rubber has better co-vulcanization effect when using zinc octadecyl isopropyl dithiocarbamate for vulcanization.
When EPDM is used together with other types of rubber to improve the physical properties and processing performance of the product, it is necessary to adjust the vulcanization system, properly adjust the production process conditions, and use the rubber to achieve co-vulcanization to further improve the performance and life of the finished rubber product.
Exclusive original article [commercial authorization] reprint, excerpt and excerpt in any form are prohibited without written authorization. Focus on Hongyun rubber: learn the process formula and raw material technology of producing rubber products from recycled rubber to help you reduce costs and increase profits