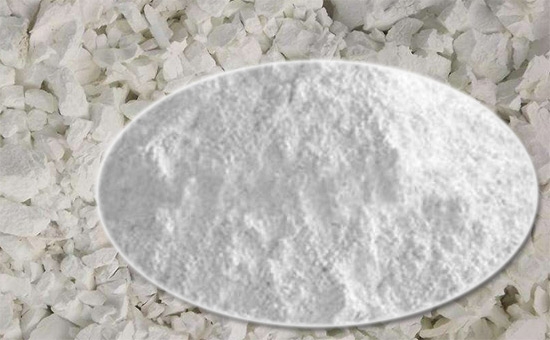
EPDM rubber has excellent resistance to high and low temperatures and aging. It can be used to produce all kinds of sealing strips with good performance and long life. In the actual production process, excessive moisture content will cause problems such as the formation of bubbles inside the extruded rubber strip, especially the EPDM rubber with high ethylene content, the moisture is difficult to volatilize, and it is necessary to use a moisture absorbent. So what is the commonly used hygroscopic agent in EPDM sealing tape? What problems should be paid attention to during use?
1. Commonly used hygroscopic agent for EPDM sealing tape
Calcium oxide is the most commonly used hygroscopic agent in the rubber products industry. It can react with water to form calcium hydroxide. If the EPDM rubber or other raw and auxiliary materials contain moisture, when choosing normal pressure vulcanization (such as microwave, salt bath, hot air drying tunnel, etc.), the moisture will vaporize during the vulcanization process, resulting in many pores in the product. Therefore, when using EPDM rubber to produce rubber sealing strips, an appropriate amount of calcium oxide is added to consume the water in the rubber.
2. Application skills of calcium oxide in EPDM strips
Calcium oxide has a fast moisture absorption rate, and the rubber compound added with calcium oxide should not be parked for too long, otherwise the calcium oxide will lose its moisture absorption effect. When EPDM sealing tape manufacturers use calcium oxide, they need to strictly seal calcium oxide 2LLYY1124 during transportation and storage. Generally, additives such as paraffin oil are used to treat or coat the surface of calcium oxide to reduce the rate of calcium oxide moisture absorption and improve storage. safety.
3. The relationship between the amount of calcium oxide and the vulcanization process
In actual production, the performance requirements and vulcanization conditions of different sealing strips are different, and there is a gap in the amount of calcium oxide.
Under normal circumstances, the choice of extruded rubber strips vulcanized at normal pressure is easy to form pores during the production process, and the amount of calcium oxide should be increased appropriately. The amount of calcium oxide in EPDM sealing strips with higher hardness or sealing rubber strips processed under vacuum conditions should be appropriately reduced. The amount of ordinary calcium oxide in the EPDM sealing strip using microwave continuous vulcanization is about 8-15 parts; the amount of calcium oxide in the sponge sealing strip is less than that in the solid sealing strip, and the dosage is controlled at 3-5 parts.
4. The relationship between the amount of calcium oxide and the mechanical properties of the sealing strip
The dispersibility and reinforcement performance of calcium oxide in the rubber compound is poor. During use, it will compete with zinc oxide to form a non-vulcanizing active substance, which reduces the crosslink density of the rubber compound and limits the increase of the crosslink density, resulting in the rubber compound The increase in compression set will affect the sealing performance and service life of EPDM sealing strips. Therefore, the amount of calcium oxide in the EPDM sealant should not be too large, as long as it meets the moisture absorption performance requirements, so as to ensure the physical and mechanical properties of the sealant and the resilience of the rubber.
At present, a certain proportion of reclaimed rubber is used in the production of many EPDM sealing strips to reduce costs. Rubber sealing strip manufacturers should pay attention to the moisture content in the reclaimed rubber when choosing reclaimed rubber, and adjust the formula appropriately according to the physical properties and dosage of the reclaimed rubber. The amount of calcium oxide can reduce the cost while ensuring the comprehensive performance of the EPDM sealing strip.
Exclusive original article [commercial authorization] reprint, excerpt and excerpt in any form are prohibited without written authorization. Focus on Hongyun rubber: learn the process formula and raw material technology of producing rubber products from recycled rubber to help you reduce costs and increase profits