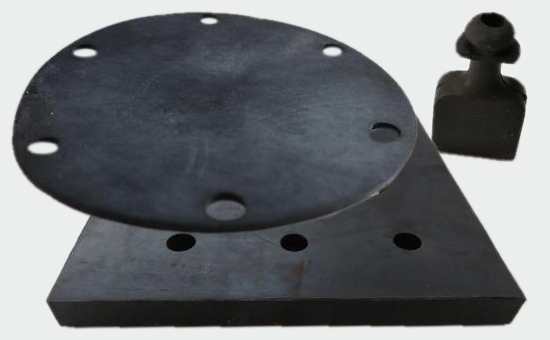
EPDM rubber has excellent high temperature resistance and ozone resistance but poor adhesion; natural rubber has good mechanical properties and processing technology properties but poor aging resistance. If natural rubber and EPDM rubber are used together in a certain proportion, the comprehensive performance of rubber products can be further improved. In actual production, the quality of vulcanized rubber directly determines the quality of finished rubber products. The co-vulcanization of two or more blends can further optimize the various indicators of the blended rubber; then can natural rubber be combined with EPDM rubber Realize co-vulcanization?
1. Definition of rubber co-vulcanization
Vulcanization is the process of adding vulcanizing system compounding agents (mainly vulcanizing agent and accelerator) to rubber, and converting linear rubber macromolecules into a three-dimensional network structure at a certain vulcanization temperature and vulcanization pressure. Rubber co-vulcanization means that under the same vulcanization conditions, different rubber phases reach the positive vulcanization point at the same time during the vulcanization process, and co-crosslinking occurs between the rubber phase interfaces. Due to the different solubility of vulcanizing agents and accelerators in various rubbers, the vulcanization speed and degree of vulcanization of each rubber phase of the combined rubber may be very different. Rubber product manufacturers need to solve this problem through the cooperation of vulcanization systems.
2. Co-vulcanization of natural rubber and EPDM rubber
In actual production, natural rubber has good compatibility with general-purpose synthetic rubbers such as styrene butadiene rubber and butadiene rubber, and has excellent rubber properties. However, there are differences in polarity, unsaturation and vulcanization activity between natural rubber and EPDM rubber: the main chain of EPDM molecule is aliphatic saturated chain, and there are no active groups and polar substituent groups inside. , The vulcanization speed is very slow; the solubility of vulcanized rubber and accelerator in NR and EPDM is different; it is difficult to achieve co-vulcanization.
3. How to realize co-vulcanization of natural rubber and EPDM rubber
The co-vulcanization of rubber is carried out under the conditions that have the basis of co-vulcanization. In actual production, it is first necessary to select a co-vulcanization system to balance and use the vulcanization speed of the rubber phase, balance the concentration distribution of the vulcanization accelerator 2LLYY722 in each rubber phase, and increase the reaction capacity of the less reactive rubber in advance. The vulcanizing agent has a high solubility in the natural rubber phase, and the natural rubber phase will quickly consume the vulcanizing agent during the vulcanization process, causing the vulcanization of natural rubber and EPDM rubber to fail to synchronize.
To achieve co-vulcanization of natural rubber and EPDM rubber, rubber products manufacturers need to solve two problems: one is to choose a suitable vulcanization accelerator to reduce the concentration difference between the two rubber phases; the second is Balance the vulcanization activity of natural rubber and EPDM rubber, and coordinate the vulcanization rate of rubber materials. Under normal circumstances, natural rubber chooses a slower vulcanization speed or a late-acting vulcanization system, which is conducive to co-vulcanization with EPDM; EPDM masterbatch adopts a fast vulcanization system, and the combination of sulfur and accelerator CZ can prepare a good comprehensive performance Natural/EPDM combined glue.
In actual production, due to the poor self-adhesiveness and mutual adhesion of EPDM, it cannot be used in rubber-metal products, which limits the expansion of EPDM rubber applications; in the formulation of EPDM rubber products Appropriate use of natural rubber can significantly improve this problem, but it takes a lot of work to achieve co-vulcanization of the two. At this time, you may wish to replace natural rubber with natural latex reclaimed rubber. Reclaimed latex retains the basic performance characteristics of natural rubber and has better compatibility with EPDM rubber. Co-vulcanization can be achieved by adjusting the vulcanization system appropriately; while reducing costs Further improve the performance of EPDM rubber products and expand the scope of application.
Exclusive original article [commercial authorization] reprint, excerpt and excerpt in any form are prohibited without written authorization. Focus on Hongyun rubber: learn the process formula and raw material technology of producing rubber products from recycled rubber to help you reduce costs and increase profits