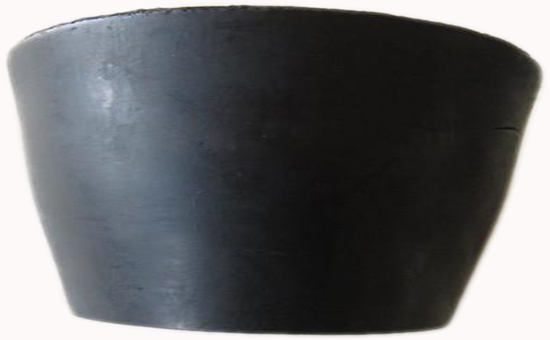
When using natural rubber to produce rubber products, rubber products manufacturers can also choose peroxide vulcanization system, ester vulcanization system or maleimide vulcanization system. After vulcanization of different vulcanization systems, the vulcanization resistance, mechanical strength, There are differences in heat resistance, fatigue resistance, etc. Natural rubber products manufacturers can choose the appropriate vulcanization system according to actual needs.
2. Peroxide curing system
Dicumyl peroxide (DCP) is the most commonly used organic peroxide curing agent. When natural rubber chooses the peroxide vulcanization system, the amount of DCP is generally controlled at 2-4 parts, and carbon-carbon bonds are formed after vulcanization. The vulcanized rubber 2YLYY519 has good high temperature resistance, good thermal stability, small creep and small compression set. Good dynamic performance and good resistance to reversion. In actual production, the DCP crosslinking agent can be used to make white, transparent and heat-resistant natural rubber products with low compression set requirements.
The following points need to be noted: the natural rubber vulcanized with peroxide has a slow vulcanization rate and is easy to scorch, the vulcanized rubber has low tear strength, is incompatible with antiozonants, and the vulcanized model is easy to foul. In addition, the decomposition products of peroxide vulcanization are not volatile, and the vulcanized rubber has a strong smell.
3. Ester curing system
Ester curing system refers to the urethane crosslinking system, the adduct of diisocyanate (TDI), MDI and p-nitrosophenol. The natural rubber vulcanizate vulcanized with ester vulcanization system has good reversion resistance, heat resistance and aging resistance, and can further improve the adhesion of natural rubber to cords, fabrics, steel wires and other materials.
4. Maleimide curing system
The maleimide vulcanization system is a high-temperature vulcanization system. The vulcanizate has good reversion resistance and thermal stability, and the vulcanizate has a small compression set and good adhesion to the glass fiber. In actual production, dithiobisphenylmaleimide and m-phenylene bismaleimide are effective.
In the production of natural rubber products, sulfur vulcanization systems are the most common, followed by peroxide vulcanization systems. Some rubber products can also use sulfur and peroxide together, which have the characteristics of both vulcanization systems. In actual production, when using sulfur vulcanization, rubber product manufacturers need to pay special attention to problems such as reversion of vulcanization. The editor has the opportunity to continue to share with you the key points of natural rubber sulfur vulcanization system.
Exclusive original article [commercial authorization] reprint, excerpt and excerpt in any form are prohibited without written authorization. Focus on Hongyun rubber: learn the process formula and raw material technology of producing rubber products from recycled rubber to help you reduce costs and increase profits