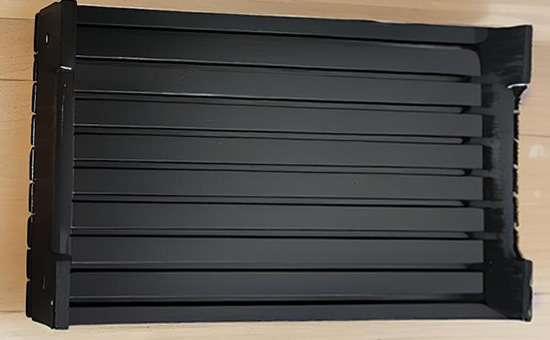
Natural reclaimed rubber is a rubber renewable resource processed from waste natural rubber and waste latex products as the main raw materials, which can directly replace part of natural rubber or be used in combination with other rubber to produce rubber products, effectively reducing the cost of raw materials. Rail damping pads are track damping pads or track isolation pads, usually made of rubber, plastic, metal or other synthetic materials, which are used to reduce the vibration and noise impact of the track structure on the surrounding environment. The rubber part of the track shock absorbing pad can use natural rubber, recycled rubber, etc., and the natural reclaimed rubber can be used alone or in combination with natural rubber to give the track shock absorbing pad good elasticity and durability.
1. The basic composition of the vulcanization formula of natural reclaimed rubber production rail damping pad
When using natural reclaimed rubber as the main raw material in the production of rail damping pads, natural reclaimed rubber can be used as a base material to improve the necessary elasticity and durability, or natural rubber can be used in combination with natural reclaimed rubber. Carbon black is used as a reinforcing agent to improve the elasticity and durability of natural reclaimed rubber track shock absorbing pads; The natural reclaimed rubber rail shock absorbing pad selects sulfur or peroxide as the vulcanizing agent, which is used to cross-link rubber molecules to improve its strength and elasticity; Softening and plasticizing systems using paraffin oil or plasticizers can effectively improve the processing performance and flexibility of rubber; The use of anti-aging system can extend the service life of natural reclaimed rubber track shock absorbing pads.
2. Optimization skills of vulcanization formula for natural reclaimed rubber production of rail damping pads
The technical parameters of rubber track damping pads mainly include hardness, tensile strength, tear strength, compression set, wear resistance, aging resistance, etc. When using natural reclaimed rubber as the main raw material to produce track shock absorbing pads, it is necessary to adjust the variety and dosage of vulcanizing agents and accelerators, as well as the ratio of reinforcing agents and softeners according to the specific use requirements of track shock absorbing pads, so as to achieve the best physical properties; Choose the right antioxidants and antioxidants to improve the weather resistance and oxidation resistance of your products.
In actual production, different types of vulcanizing agents (such as sulfur, peroxide, metal oxide, etc.) have different effects on the crosslinking density; An increase in the amount of vulcanizing agent usually increases the crosslinking density, and too much can lead to a decrease in rubber performance due to excessive crosslinking. Accelerators can accelerate the vulcanization reaction, and different types of accelerators have different effects on the vulcanization rate and crosslinking density. Reinforcing agents (e.g., carbon black) and fillers (e.g., calcium carbonate) can affect the vulcanization behavior and crosslinking density of rubber. Excessive use of softeners and plasticizers will reduce the crosslinking density.
2. The production process and key points of natural reclaimed rubber production track shock absorbing pad
The main process of natural reclaimed rubber for the production of rail damping pads is mixing, forming and vulcanization.
Mixing: It is to mix natural reclaimed rubber with various additives evenly.
Molding: The mixed rubber material is molded into the desired shape of the rail damping pad.
Vulcanization: Vulcanization is carried out at a certain temperature and pressure to achieve the desired physical properties of the rubber.
During the curing process, controlling the vulcanization temperature and time is essential to achieve the best track cushion performance. The control of vulcanization temperature and time can affect the crosslink density, physical properties and durability of rubber. When vulcanizing the natural reclaimed rubber rail shock absorbing pad, it is necessary to determine the optimal vulcanization temperature and vulcanization time.
The determination of the vulcanization temperature is usually based on the vulcanization system used (e.g., sulfur or peroxide vulcanization) as well as the rubber formulation.
Too high a temperature can lead to excessive cross-linking, making the rubber hard and brittle, while too low a temperature can lead to insufficient cross-linking and insufficient strength and elasticity of the rubber. Typically, the vulcanization temperature is adjusted within the recommended vulcanization temperature range of the rubber to obtain the best physical properties.
Vulcanization time refers to the amount of time the rubber is held at the vulcanization temperature to ensure the desired degree of cross-linking. A vulcanization time that is too short may result in incomplete cross-linking, while too long a time may result in excessive cross-linking. The determination of the vulcanization time is usually optimized by experiment and experience, and can be assisted by the vulcanization curve (i.e., the graph of the vulcanization time versus the degree of vulcanization).
Ensure that the temperature and time distribution within the mold during vulcanization is uniform to avoid local pervulcanization or undervulcanization. Proper heating and cooling systems are used, as well as mold design, to ensure temperature and time control during the vulcanization process. In order to further improve the properties of the rubber, it may be necessary to carry out a post-vulcanization treatment, which keeps the rubber at a certain temperature for a period of time after vulcanization to further complete the cross-linking.
There are still many things that need to be paid attention to when using natural reclaimed rubber as the main raw material to produce rail damping pads, and we will continue to discuss related topics with you in the future.
Exclusive original article [commercial authorization] reprint, excerpt and excerpt in any form are prohibited without written authorization. Focus on Hongyun rubber: learn the process formula and raw material technology of producing rubber products from recycled rubber to help you reduce costs and increase profits