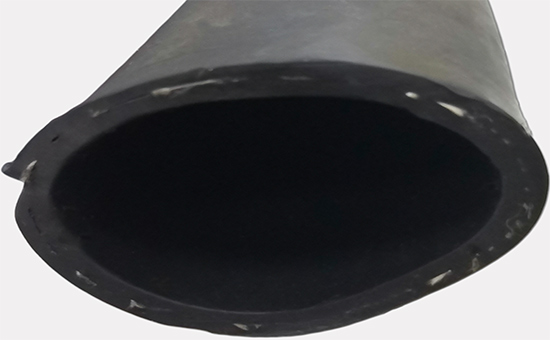
Rubber pipes are processed with rubber as the main material, and can be used to transport various gases, gases, viscous fluids, solid particles, etc., and are widely used in industry and agriculture, transportation, energy and other fields; Low-cost replacement raw materials for rubber can be used in the production of various types of hoses, effectively reducing the cost of raw materials. When using reclaimed rubber to produce rubber pipes in the rainy season, the problem of foaming and delamination is prone to occur. Why? How to effectively eliminate the phenomenon of foaming and delamination of reclaimed rubber hose? The editor will discuss this issue with you in detail today from both internal and external factors.
1. Internal factors: control the moisture content, the reclaimed rubber hose is not easy to foam and delaminate in the rainy season
In the rainy season, the relative humidity of the air exceeds 70%, and the problem of foaming and delamination is easy to occur in the production process of the reclaimed rubber hose. It is necessary to strictly control the moisture content. Specifically, the following points should be done:
(1) Dry the canvas to reduce the moisture content of the canvas to below 1.5%.
(2) Drying pads: The moisture content of the pads in the rainy season is controlled at about 7%. Using the pads will make the rubberized canvas absorb moisture quickly, and the moisture content of the rubberized canvas is about 5%; therefore, the pads need to be dried. , and try to delay the use on the shift and judge the use on the shift as much as possible.
(3) Wipe the tape and send it to the drying room.
In the production process of the reclaimed rubber hose in the rainy season, it is necessary to strictly control the moisture content of various compounding agents, strictly control the moisture content of the textile, and strictly implement the process to effectively avoid the phenomenon of foaming and delamination of the rubber hose in the rainy season.
2. External factors: control the process conditions, the reclaimed rubber hose is not easy to foam and delaminate in the rainy season
(1) Vulcanization point
In the production process of reclaimed rubber hose, the delamination among cloth layers has a great relationship with the slow vulcanization point of rubbing rubber. If there are cloth folds, burrs, oil stains, dust, etc. attached, it is easier to delaminate. During the vulcanization process of the reclaimed rubber hose, the heating conditions of the inner, outer and rubbing layers are different. It is necessary to correctly match the vulcanization speed to form synchronous vulcanization, so that the components can be well combined; otherwise, it is easy to occur at the interface with different vulcanization speeds. Foam delamination.
In actual production, the initial sulfur point of reclaimed rubber hose should be 4-4.5min, the positive vulcanization point should be 10-15min, the initial sulfur point of the inner rubber should be 4.5-5.5min, and the positive vulcanization point should be 13-18min. The initial sulfur point of the outer rubber is 5.5-6.5min, and the positive vulcanization point is 18-23min.
(2) The air pressure and temperature in the vulcanization tank should be consistent
During the vulcanization process of the reclaimed rubber hose, the air pressure in the vulcanization tank is quite different, resulting in a local low pressure area, and the steam in the hose body will accumulate in the weak link of the low pressure and low temperature section, causing foaming and delamination. During vulcanization, especially in the early stage of vulcanization, if there is a pressure drop, the balance of pressure inside and outside the pipe will be destroyed, resulting in the problem of foaming and delamination. Therefore, during the vulcanization process of the reclaimed rubber hose, the steam pressure must be kept stable and cannot be lowered, and only water is released but not steam. After the reclaimed rubber hose is vulcanized on time, in order to prevent the expansion of foaming and delamination caused by the rapid withdrawal of steam pressure, cold air should be adopted when the vulcanization is on time, and cold water should be sprayed in the tank to strengthen cooling.
When using reclaimed rubber to produce cost-effective hoses, be sure to ensure that the cloth layer is flat, no whitening, no cloth folds, no burrs or hard edges, no glue lumps, no dust and oil stains, no volatile gasoline during molding, and the surface of the inner rubber cylinder. There are no small water droplets, the inflation size is appropriate during molding, the fitting pressure is uniform, the tube body is not deformed during the processing of semi-finished products, etc. Even in the rainy season, the phenomenon of foaming and delamination of the rubber tube is not easy to occur; otherwise, the air humidity is not high. In high seasons, it is difficult to eliminate the problem of blistering and delamination.
Exclusive original article [commercial authorization] reprint, excerpt and excerpt in any form are prohibited without written authorization. Focus on Hongyun rubber: learn the process formula and raw material technology of producing rubber products from recycled rubber to help you reduce costs and increase profits