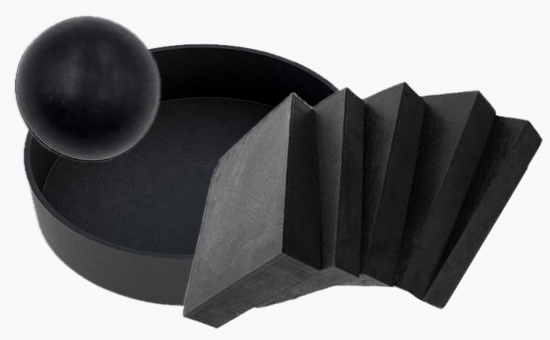
The early vulcanization of the rubber material during the processing operation or storage process is scorch. Elastic lumps will appear on the surface of the scorched rubber, which increases the load of processing equipment and affects the appearance quality and mechanical strength of rubber products. When using latex reclaimed rubber to produce rubber products, especially when used with natural rubber, properly adjusting the scorch time of reclaimed rubber can further improve the quality of rubber products and increase the yield.
The scorch time is an index to measure the difficulty of scorching of the rubber compound. The longer the scorch time, the less likely to occur early vulcanization. The main cause of scorch is improper selection of vulcanization system. In actual production, adjusting the scorch time of rubber material 2YLYY46 also needs to consider the vulcanization efficiency of latex reclaimed rubber. Rubber product manufacturers generally start with two aspects: accelerator and anti-scorching agent.
1. Promoter selection skills
When selecting the accelerator in the latex reclaimed rubber vulcanization system, the scorch performance of the accelerator itself should be fully considered, and the structure should contain anti-scorch functional groups (-SS- etc.) and auxiliary anti-scorch groups (such as carbonyl, carboxyl, sulfonyl) , Phosphoryl, benzothiazolyl, etc.). In actual production, when adjusting the scorch time of reclaimed latex rubber, an accelerator with a higher delay effect or a higher critical temperature should be selected as far as possible.
2. Common accelerator scorch performance
Sulfonamide accelerators have long scorch time, fast vulcanization rate, flat vulcanization curve, good overall performance, and high processing safety. The thiuram accelerator TMTD has a short vulcanization induction period and can quickly vulcanize the rubber. To prevent scorching, TMTD is often used in combination with sulfenamide accelerator CZ and thiazole accelerator DM. In actual production, manufacturers of latex reclaimed rubber products usually use two or more types of accelerators together to further adjust the scorch time of reclaimed rubber to ensure rubber production efficiency and processing safety.
The scorch time of common accelerators increases in sequence according to the following order: ZDC<TMTD<M<DM<CZ<NS<NOBS<DZ. It should be noted that the combined use of accelerator CZ, accelerator DM, accelerator D, and dithiocarbamate will cause the latex reclaimed rubber to have worse scorch resistance.
3. Tips for using anti-scorching agent
Anti-scorch agent is a special additive to prevent early vulcanization of rubber during processing. Common anti-scorch agents include benzoic acid, salicylic acid, phthalic anhydride, N-nitroso diphenylamine, etc., generally based on actual conditions. Need to choose a suitable anti-scorching agent.In actual production, the amount of anti-scorching agent is about 0.1-0.5 parts.
It should be noted that the commonly used phthalic acid glycosides are low in price but difficult to disperse in the rubber, resulting in the decrease of the mechanical strength of the rubber and the effect of delaying vulcanization; phthalic anhydride contains sulfenamide accelerators and thiazoles. The anti-scorching effect of the accelerator-like rubber compound is not obvious. N-nitroso diphenylamine has a good scorch prevention effect in rubber compounds using sulfenamide accelerators, but the activity decreases when the processing temperature exceeds 100°C, the scorch prevention effect is small at 120°C, and it loses its activity at 135°C and decomposes the released gas Easy to form pores.
Adjusting the scorch time of reclaimed latex rubber, the variety and dosage of reinforcing fillers, and the design of the anti-aging system will also affect the scorch time. When combined with other types of rubber, the type of rubber used will also affect the scorch time. The follow-up editor will continue to share with you the related issues of adjusting the scorch time of latex reclaimed rubber.
Exclusive original article [commercial authorization] reprint, excerpt and excerpt in any form are prohibited without written authorization. Focus on Hongyun rubber: learn the process formula and raw material technology of producing rubber products from recycled rubber to help you reduce costs and increase profits