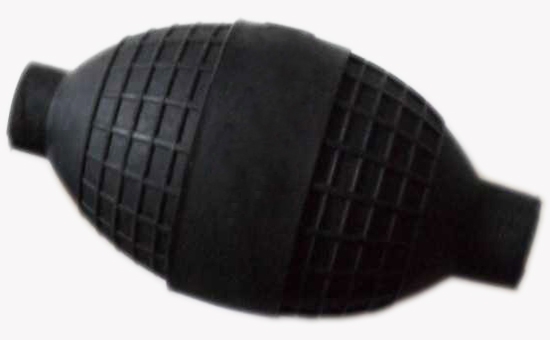
The combined use of natural rubber and butadiene rubber can produce rubber products with high mechanical strength, good elasticity, excellent wear resistance, low temperature resistance, and low dynamic load. Latex reclaimed rubber is a low-cost exchangeab raw material for natural rubber, directly replacing natural rubber and butadiene rubber to produce rubber products with low cost and good performance. When using butadiene rubber/latex reclaimed rubber and rubber materials to produce rubber products, the blending effect of the two rubber materials directly affects the quality of the finished rubber products.
1. Blending method of butadiene rubber and latex reclaimed rubber
In actual production, there are two main blending methods for the combined use of butadiene rubber and reclaimed latex rubber, one is the direct blending method, and the other is the masterbatch blending method. ①Direct blending method: The butadiene rubber and the reclaimed latex rubber are blended into the wrap roll with a thin roll pitch of 2YLYY325 using an open mill and then mixed in a conventional manner. ②Masterbatch blending method: The reclaimed latex rubber is made into a masterbatch, and then added as a compounding agent when the butadiene rubber is conventionally mixed, and the mixing is uniform; the general mixing temperature is controlled at 50°C.
2. The characteristics of different blending methods of butadiene/latex regeneration
(1) Direct blending method: The butadiene rubber/latex reclaimed rubber combined with the direct blending method has a faster vulcanization speed, a slight increase in hardness, a decrease in elongation at break, high shear stress, poor fluidity, and roll-coated properties. Inferior, the surface of the compound is rough and has no stickiness.
(2) Masterbatch blending method: the butadiene rubber/latex reclaimed rubber using the masterbatch blending method speeds up the vulcanization process, improves the hardness of the rubber, and has good roll-wrapping properties during mixing. The surface of the mixed rubber is smooth and has a touch. Viscosity, low die expansion value; used for extruding products in the production of extruded rubber with smooth surface and stable size.
3. The efficiency of butadiene/latex regeneration using masterbatch blending method
Generally, when the masterbatch blending method is adopted, the mixing time of latex reclaimed rubber masterbatch is about 8-12 minutes, which is not much different from the time used by the direct blending method. It will speed up the vulcanization process to a certain extent, and will not affect the overall Productivity.
In actual production, butadiene rubber and latex reclaimed rubber can be used together, or butadiene rubber/natural rubber/latex reclaimed rubber can be used together, and butadiene rubber/natural rubber/styrene butadiene rubber/latex reclaimed rubber can also be used together to produce Rubber products with better comprehensive performance and lower cost. Choosing an appropriate blending method in the production process can further optimize the quality of the finished product and extend the service life of the rubber product; the editor has the opportunity to continue to discuss with you the specific types of rubber products produced by the combined use of butadiene rubber and latex reclaimed rubber.
Exclusive original article [commercial authorization] reprint, excerpt and excerpt in any form are prohibited without written authorization. Focus on Hongyun rubber: learn the process formula and raw material technology of producing rubber products from recycled rubber to help you reduce costs and increase profits