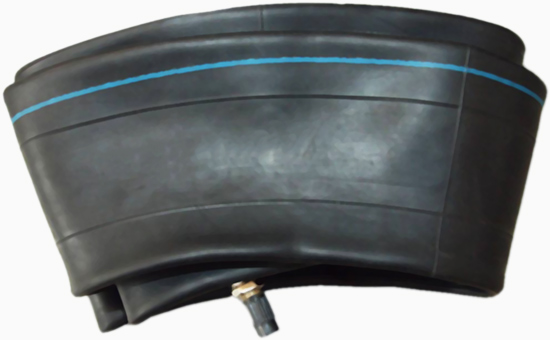
The rubber inner tube was originally processed with natural rubber as the main raw material; butyl rubber has excellent air tightness, heat resistance, good elasticity, aging resistance, etc., and can better meet the needs of inner tubes. Therefore, most vehicle inner tubes on the market are currently on the market. Both were replaced by butyl inner tubes. Butyl reclaimed rubber has better compatibility with other rubbers, and can be used with natural rubber to produce vehicle inner tubes, reducing costs and improving the air tightness and heat resistance of the inner tube products. Butyl reclaimed rubber can also be used in combination with butyl rubber to produce more cost-effective butyl inner tubes.
1. A large number of butyl reclaimed rubber and natural rubber are used together to produce rubber inner tube formulations
40 parts of natural rubber, 60 parts of butyl reclaimed rubber, 6.5 parts of zinc oxide, 3.5 parts of stearic acid, 1 part of antioxidant A, 2 parts of antioxidant RD, 25 parts of carbon black N330, 15 parts of carbon black N774, 10 parts of activated calcium carbonate parts, 8 parts of pine tar, 1.3 parts of sulfur, 0.6 part of accelerator M, 0.2 part of accelerator D; total: 173.1 parts.
2. Butyl reclaimed rubber and butyl rubber are used together to produce high-quality inner tube formulations
90 parts of butyl rubber, 20 parts of butyl reclaimed rubber, 5 parts of zinc oxide, 1 part of stearic acid, 35 parts of carbon black N550, 25 parts of carbon black N774, 19 parts of paraffin oil, 0.5 parts of accelerator DM, accelerator TMTD 0.9 parts, 1.5 parts of sulfur; total: 197.9 parts.
70 parts of butyl rubber, 55 parts of butyl reclaimed rubber, 5 parts of zinc oxide, 1 part of stearic acid, 35 parts of carbon black N550, 15 parts of carbon black N774, 20 parts of paraffin oil, accelerator M 0.5 parts, accelerator TMTD 1 part, 1.7 parts of sulfur; total: 204.2 parts.
3. The technological process of producing vehicle inner tube from butyl reclaimed rubber
The inner tube manufacturing process mainly includes processing procedures such as rubber cushion valve manufacturing, rubber material filtration, rubber cylinder extrusion, inner tube forming and inner tube vulcanization.
The inner tube process flow is: inner tube rubber hot refining → filtration → adding sulfur → unloading, cooling → hot refining before extrusion → extruding the tire barrel → cooling, storage → molding (fixing length, sticking valves, joints) → setting → vulcanization → Inspection. For example: when butyl reclaimed rubber/natural rubber is used to produce vehicle inner tubes, all ingredients can be mixed in an internal mixer at a mixing temperature of about 140 °C; then filtered through a rubber filter and pressed out by an extruder, Fixed length, attached to the mouth; then jointed by a joint machine; vulcanized by a vulcanizing machine, and the vulcanization temperature is controlled at about 150 °C.
Compared with butyl rubber, butyl reclaimed rubber has a faster vulcanization speed and better compatibility with other varieties of rubber. It can be used alone or in combination with butyl rubber, natural rubber, styrene-butadiene rubber and other rubbers to produce Rubber 2ELYY33 inner tubes with different technical indicators meet the actual needs of different vehicles for inner tubes. Later, the editor will have the opportunity to continue to share with you the specific application skills of butyl reclaimed rubber in rubber inner tubes.
Exclusive original article [commercial authorization] reprint, excerpt and excerpt in any form are prohibited without written authorization. Focus on Hongyun rubber: learn the process formula and raw material technology of producing rubber products from recycled rubber to help you reduce costs and increase profits