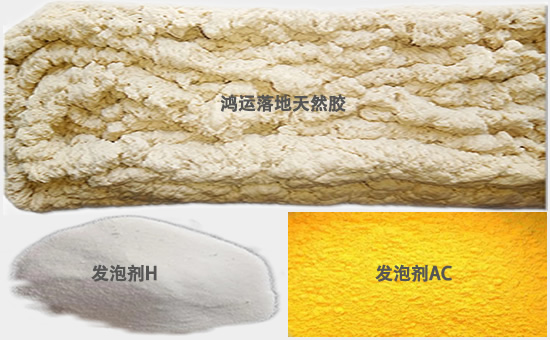
Sponge foam rubber is a porous structural material with perforations throughout the entire material. According to the structure of the pores, sponge rubber can be divided into three types: open pores (with interconnected pores), closed pores (with pores separated by the pore walls and not interconnected), and mixed micropores (with both open and closed pores). Sponge foam rubber products have excellent elasticity, flexibility, shock absorption, sound insulation, and thermal insulation properties, while also having a low density
The rubber material used for manufacturing sponge rubber needs to meet the following requirements:
1. The adhesive should have appropriate plasticity. The plasticity of the rubber material is closely related to factors such as the density, pore structure and size, and foaming rate of sponge rubber. The rubber material of sponge rubber should have a Vickers plasticity of not less than 0.5. During the processing, special attention should be paid to the plasticization of raw rubber, especially when dealing with high viscosity raw rubber such as latex recycled rubber, tire recycled rubber, sub brand natural rubber, nitrile rubber, etc., 3 or 4 stages of plasticization should be used, and the number of thin passes can be up to 30-50
2. The foaming rate of the recycled rubber material should match the vulcanization rate
3. The heat transfer performance of the recycled rubber material should be excellent to ensure uniform internal and external foam pores and consistent vulcanization degree
4. During foaming, the internal pressure of the recycled rubber material should be greater than the external pressure
Choosing a suitable type of sponge rubber adhesive needs to consider the product's usage conditions. Ordinary sponge rubber can use natural rubber, styrene butadiene rubber, cis-1,4-polybutadiene rubber, etc., while lower grade ones can use latex recycled rubber, tire recycled rubber, etc. If you need oil resistance, you can choose nitrile rubber, chloroprene rubber, nitrile rubber/polyvinyl chloride, epoxidized natural rubber, etc. If heat resistance and ozone aging resistance are required, EPDM rubber and silicone rubber can be selected. When manufacturing microporous soles, EVA or high styrene can be used in conjunction with universal rubber, or nitrile rubber can be mixed with polyvinyl chloride
Natural rubber, styrene butadiene rubber, polybutadiene rubber, and their mixtures with plastics are commonly used to manufacture civilian sponge rubber products, while EPDM and chloroprene rubber are mostly used to manufacture industrial sponge rubber products. From the comprehensive consideration of service life, process, cost, and other aspects, EPDM recycled rubber and chloroprene rubber are ideal rubber materials for making sponge rubber
Rubber foaming agents should meet the following requirements 23Y5Y11:
① Good storage stability, stable to acid, alkali, light, and heat
② Non toxic, odorless, harmless to the human body, non polluting after foaming, without odor or odor
③ Low heat generated during decomposition
④ Able to complete decomposition in a short period of time, with large and adjustable gas generation capacity
⑤ The particle size is uniform and easy to disperse, and the particle shape is preferably spherical
⑥ It can be fully decomposed in a closed mold cavity
Rubber foaming agents are indispensable materials in the production of sponge foam rubber products, and they can be divided into two types: organic and inorganic. Organic rubber foaming agents include azo compounds (such as foaming agent AC, azodiisobutyronitrile, etc.), sulfonyl hydrazine compounds (such as benzene sulfonyl hydrazine, p-toluene sulfonyl hydrazine, etc.), nitroso compounds (such as foaming agent H, etc.) and urea based compounds (such as urea, Tosyl urea, etc.). Inorganic rubber foaming agents mainly include ammonium carbonate, sodium bicarbonate, sodium carbonate, ammonium chloride, sodium nitrite, etc
The decomposition of inorganic foaming agent is a endothermic reaction and belongs to alkaline substances, so the sulfur generation rate is fast. The initial decomposition temperature is low, and the components of the decomposed gas are carbon dioxide and water, resulting in a high proportion of continuous bubbles. The decomposition temperature of organic foaming agents is generally high, and the gas released during decomposition is mainly nitrogen, which is suitable for manufacturing sponge products with closed cell structures
The decomposition temperature of foaming agents such as H and AC is relatively high, and they cannot decompose foam at normal vulcanization temperatures. Therefore, foaming additives can be added to reduce the decomposition temperature, help disperse the foaming machine, or increase gas generation. Commonly used foaming aids include organic acids, urea, and their derivatives. The former includes stearic acid, oxalic acid, boric acid, benzoic acid, salicylic acid, etc., and is often used as an auxiliary agent for foaming agent H. The latter includes organic salts such as zinc oxide and borax, which are often used as additives for foaming agent AC, but the decomposition temperature can only be reduced to around 170 ℃. When using foaming agents, attention should be paid to the impact on the vulcanization rate of rubber. We need to optimize the vulcanization formula of sponge rubber to ensure that the vulcanization rate of the rubber material matches the decomposition rate of the foaming agent
Different types of rubber require different vulcanization formulas to be selected. General rubber, such as latex recycled rubber, tire recycled rubber, floor natural rubber, styrene butadiene rubber, cis-1,4-polybutadiene rubber, etc., adopts a sulfur accelerator vulcanization formula with a sulfur content of 1.5-3 parts. Promoters M, DM, CZ, DZ, TMTD、PZ, etc. can be used alone or in combination as accelerators for sponge rubber, but the dosage is more than that of solid products. Silicone rubber, EPDM recycled rubber, nitrile recycled rubber, EVA, rubber plastic alloys, and some rubber plastic blends can use peroxide vulcanization formula. The amount of peroxide should be calculated based on the cross-linking efficiency of the polymer, and the increase or decrease in its amount can only control the cross-linking density. The curing time of peroxide vulcanization should be determined based on its half-life at the curing temperature, usually 5-10 times the half-life at the curing temperature. Chloroprene rubber commonly uses zinc oxide and active magnesium oxide as vulcanizing agents, and NA-22 as accelerator
The selection of fillers in sponge foam rubber should have the following characteristics: low density, good dispersion, no hardening of the rubber material, the ability to adjust the plasticity and flowability of the rubber material, and contribute to the foam process of the sponge. Various fillers have little effect on the decomposition temperature and rate of foaming agents, but they are very important for improving the strength, durability, processing performance, uniformity of microporous structure and distribution, and cost of rubber sponges. The dispersibility of fillers is very important, as the uniform dispersion of their particles can promote the formation of porous billets, which is related to the uniformity of foaming and the surface appearance of products. Dispersed fillers include semi reinforced carbon black, easily mixed tank black, and lightweight calcium carbonate
Exclusive original article [commercial authorization] reprint, excerpt and excerpt in any form are prohibited without written authorization. Focus on Hongyun rubber: learn the process formula and raw material technology of producing rubber products from recycled rubber to help you reduce costs and increase profits