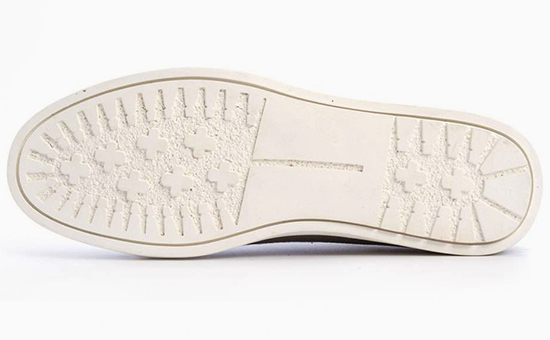
The rubber outsole has good elasticity, wear resistance and bending resistance. Generally, natural rubber and styrene-butadiene rubber are used as the main raw materials. The use of proper amount of reclaimed rubber in the rubber outsole can reduce the raw material cost and production energy consumption. It is commonly used by many rubber sole processing enterprises. Means; when using light-colored reclaimed rubber to produce light-colored rubber outsole, not only need to pay attention to the type and amount of reclaimed rubber, but also pay attention to the color, performance, characteristics and matching skills of various compounding agents in the light-colored reclaimed rubber outsole.
Among the reclaimed rubber products, only white latex reclaimed rubber can be used in the production of light-colored rubber outsole. According to the basic performance characteristics of latex reclaimed rubber and its combination with natural rubber and styrene-butadiene rubber, the compounding agent in the formula is reasonably selected. Just fine.
1. Select the problem that the compounding agent in the light-colored reclaimed rubber outsole vulcanization system needs to be considered.
The selection of a suitable vulcanization system during the production process of the reclaimed rubber outcrop can impart good physical and mechanical properties, vulcanization flatness and anti-coke property to the rubber compound. The light-colored reclaimed rubber outsole also requires the accelerator to be non-contaminating, non-discoloring or non-discharging. Generally, a promotion system in which the promoter M/D/DM is used together or a promoter M/D/CZ may be used in combination. The accelerator M/D/DM system is commonly used in the light reclaimed rubber outsole, wherein the combined ratio of the promoter M+ accelerator DM/D is generally controlled at 65:35, or 70:30, 60:40; The ratio of M or accelerator DM to accelerator D is typically 60:40.
2. Selection techniques of various compounding agents in light-colored reclaimed rubber outsole reinforcing filling system
The amount of the compounding agent in the rubber reinforcing filling system is limited to the amount of rubber. Therefore, the color of the reinforcing agent and the filler directly affects the color of the light-colored reclaimed rubber outsole, and generally uses non-polluting white carbon black, white Yanhua, clay, and lignin. Etc.; in the reclaimed rubber outcrop system containing white carbon black combined with DEG, PEG and other active agents, clay can be activated with stearic acid.
3. Light-colored reclaimed rubber outsole softening plasticizing system Which compounding agent should be used, what are the characteristics?
Softeners and plasticizers commonly used in the production of rubber outsole include Gumalon, second-line oil, engine oil, pine tar, paraffin oil, naphthenic oil, petrolatum, spindle oil, etc., among which light-colored reclaimed rubber is used in large soles. Non-polluting petroleum softeners, such as paraffin oil, naphthenic oil, spindle oil, petrolatum, calcium base grease, etc.; when reclaimed rubber/natural rubber/styrene-butadiene rubber is used together to produce light-colored reclaimed rubber outsole and styrene-butadiene rubber When large, it can be added with 2-4 parts of terpene resin or xylene resin to increase the viscosity of the rubber.
In order to prevent discoloration of the light-colored reclaimed rubber outsole, the amount of the compounding agent in the softening plasticizing system needs to be controlled to be less than 5 parts, and the rubber oil which is highly polluting such as coal tar and pine tar cannot be used.
4. Light-colored reclaimed rubber outsole needs reasonable use of anti-aging agent and anti-focus agent
When using reclaimed rubber to produce a light-colored reclaimed rubber outsole, the anti-aging agent can delay the aging time of the rubber outsole, and the scorch prevention agent can effectively avoid the early vulcanization problem of the rubber outsole. Among them, the anti-aging agent commonly used in the light-colored reclaimed rubber outsole has non-polluting anti-aging agents MB, SP, DOD, 246, 2246, etc., to ensure that the light-colored reclaimed rubber outsole is bright. The scorch retardant commonly used in the production of light reclaimed rubber outsole is CTP.
When using reclaimed rubber to produce a light-colored reclaimed rubber outsole, not only the type of compounding agent needs to be paid attention to, but also the amount of the compounding agent needs to be appropriately adjusted according to the reaction between the compounding agents. For example, reinforcing fillers such as white carbon black and clay are used to vulcanize the reclaimed rubber. Delayed action, so the amount of sulfur should be increased appropriately, controlled between 2.2-2.6 parts, the use of accelerator D should not be too high to avoid contamination and discoloration.
Exclusive original article [commercial authorization] reprint, excerpt and excerpt in any form are prohibited without written authorization. Focus on Hongyun rubber: learn the process formula and raw material technology of producing rubber products from recycled rubber to help you reduce costs and increase profits