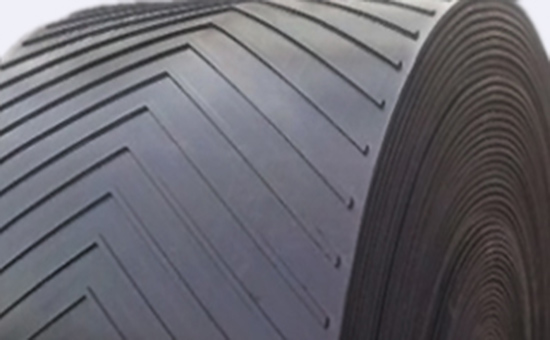
In the rubber industry, in order to improve the comprehensive performance of rubber materials or reduce costs, rubber technology is widely used. When rubber is used together, co-vulcanization can ensure that the combined rubber compound is evenly cross-linked during the vulcanization process, so as to obtain ideal mechanical properties; In the combined glue, it is very important to choose a suitable vulcanization system to achieve co-vulcanization; Sometimes it may be necessary to design a vulcanization system to ensure that all components are properly crosslinked.
1. The importance of co-vulcanization
On the one hand, co-vulcanization means that the two colloidal phases have nearly the same vulcanization rate; On the other hand, it refers to the co-cross-linking at the interface of the two colloids. Two or more rubbers can be vulcanized synchronously in the process of combined use to form a uniform cross-linking network; It is essential to ensure the mechanical properties of the compound. The realization of co-vulcanization requires that the individual components in the adhesive have similar vulcanization rates and can form effective co-crosslinks at the interface.
2. The vulcanization speed of the combined rubber needs to be matched
The matching of vulcanization rates is the basis of co-sulfidation. Different rubber components may respond differently to the same vulcanization system, so choosing the right vulcanization system so that the vulcanization rate of each component is as close as possible is the key to obtaining a good co-vulcanization effect. For example, in the combined systems of NR/SBR, NR/EPDM, NR/NBR, etc., the proximity of the vulcanization rate can bring higher constant tensile stress, elongation and tensile strength, and reduce the heat generation during the vulcanization process.
3. The process conditions affect the performance of rubber and glue
In actual production, vulcanization temperature, time, pressure, etc. will have a significant impact on the vulcanization process and final performance of the combined glue. For example; In the (CM/NA-22)/(NBR/sulfur) combined system, the dynamic vulcanization of CM is carried out first, and then the static vulcanization of NBR is carried out to obtain high tensile strength. It can be seen that the sequence and conditions of the vulcanization process have an important impact on the performance of the combined glue.
4. Commonly used rubber and glue vulcanization system selection
The selection of the vulcanization system needs to consider the solubility and dispersion coefficient of the vulcanizing agent in different rubbers, as well as their crosslinking efficiency to the rubber. For example, when EPDM rubber is used in combination with butyl reclaimed rubber, when DCP is used as a vulcanizing agent, DCP may lead to RIIR cracking; In this case, it is recommended to use EPDM with DCP and RIIR with sulfur/accelerator to achieve better co-sulfurization effect.
In addition, for specific rubber combination systems, it may be necessary to optimize the vulcanization system experimentally. For example, when CSM/SBR is used together, epoxy resins can effectively vulcanize CSM, but the crosslinking efficiency of SBR is low. However, DCP has a high crosslinking efficiency for SBR, so a good co-vulcanization effect can be obtained by using (CSM/epoxy)/(SBR/DCP) masterbatch blending strategy.
Rubber is used as a common material performance improvement method in the rubber industry, through the mixing of two or more different rubber materials together, to improve the wear resistance, oil resistance, heat resistance, cold resistance, etc., or increase the mechanical strength of the rubber 2SLYY1113 material; Mixing less expensive rubber with more expensive rubber can reduce material costs without sacrificing critical performance; The combination of certain rubbers can improve the efficiency and convenience of processes such as compounding, extrusion, and calendering.
At present, the combination of raw rubber and suitable varieties of reclaimed rubber is the main way for rubber product manufacturers to reduce costs, such as natural rubber mixed with part of the latex reclaimed rubber, tire reclaimed rubber, butyl rubber and butyl reclaimed rubber, ethylene propylene reclaimed rubber combined, EPDM reclaimed rubber instead of part of EPDM, nitrile rubber with part of nitrile reclaimed rubber replacement, can achieve the purpose of improving the physical properties of rubber and processing performance, reducing the cost of raw materials. The editor will discuss relevant issues with you in the future.
Exclusive original article [commercial authorization] reprint, excerpt and excerpt in any form are prohibited without written authorization. Focus on Hongyun rubber: learn the process formula and raw material technology of producing rubber products from recycled rubber to help you reduce costs and increase profits