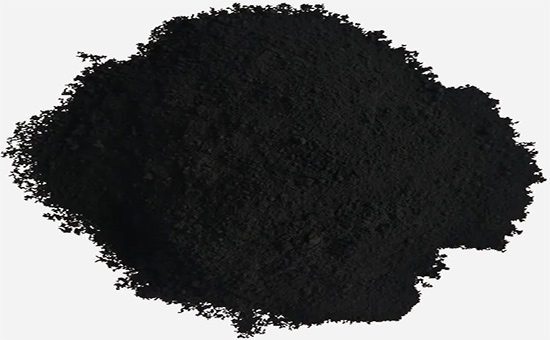
When using recycled rubber to produce rubber products, the quality of the blending agent directly affects the quality of the mixed rubber, and then affects the quality of the finished product. In actual production, if impurities are contained in the formulation, it will not only reduce the physical and mechanical strength of the reclaimed rubber vulcanizate, but also cause production accidents in serious cases. In addition, for low melting point compounds, liquid compounds, and compounds that are not easily dispersed, appropriate treatment is required before mixing. Today, the editor will continue to discuss with you other methods for supplementing unqualified compounds before mixing recycled rubber.
3. Supplementary processing of recycled rubber mixture - screening
The purpose of screening the recycled rubber mixture before mixing is to remove mechanical impurities mixed in the mixture, such as sand particles, wood chips, and large particles of the mixture itself. In actual production, mixing these mechanical impurities and coarse particles into the rubber not only reduces the physical and mechanical properties of the reclaimed rubber vulcanizate, but also can cause extremely harmful consequences: for example, mixing items such as bolts, nuts, and weights into the mixing agent can damage the mixing equipment, etc; The presence of impurities in rubber products in equipment and instruments used under high voltage can cause personal accidents.
4. Supplementary processing of recycled rubber mixture - melting, filtration, and evaporation (dehydration)
Solid softeners with low melting points and liquid softeners with high viscosity are used in the production of recycled rubber products. It is recommended to heat and melt or reduce viscosity by heating, and then filter 2SLYY323 with a special screen to remove mechanical impurities. Filtration should be performed while hot after melting or heating. If the moisture content in the liquid formulation exceeds the specified technical standards, special heating and evaporation dehydration should also be carried out; At the same time, filtration is also performed to remove mechanical impurities.
5. Supplementary processing of recycled rubber mixture - preparation of master rubber and paste
When there is a large amount of complex agent that is not easy to disperse in the reclaimed rubber, in order to make the complex agent easy to disperse, prevent agglomeration, and reduce mixing
To improve the mixing and processing environment, certain additives such as carbon black, promoters, and colorants can be made into a master compound or paste before mixing, and then mixing can be carried out; In production, carbon black and accelerants are often used to prepare master compounds, and zinc oxide, sulfur, accelerants, and colorants are also used to prepare master compounds.
The manufacture of master rubber is carried out on a rubber mixer. During manufacturing, the mixing agent and raw rubber used shall be uniformly mixed in a rubber mixer according to a certain proportion. The filling amount of the blending agent in the master rubber can be determined according to needs. For carbon black masterbatch rubber, the maximum filling amount of carbon black should not exceed its "critical concentration"; When the critical concentration is exceeded, large agglomerations and poor dispersion will occur in the master compound.
Before the mixing process of recycled rubber products, various compounding agents need to be accurately weighed and blended. The editor will continue to discuss relevant issues with you later.
Exclusive original article [commercial authorization] reprint, excerpt and excerpt in any form are prohibited without written authorization. Focus on Hongyun rubber: learn the process formula and raw material technology of producing rubber products from recycled rubber to help you reduce costs and increase profits