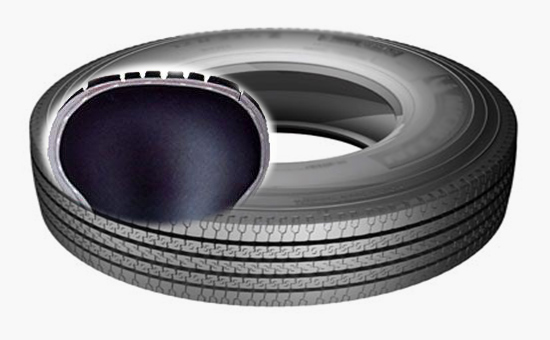
The tire inner liner is a new term after the appearance of tubeless tires. It refers to the innermost material of tubeless tires. It is the breathable rubber layer in contact with the bead in the tubeless tire. The main role in the tubeless tire is to prevent it. Compressed gas leaks. At present, the inner liner of tires on the market is generally produced from chlorinated butyl rubber with excellent vulcanization properties and excellent air tightness and high elasticity natural rubber. As a material processed from waste butyl rubber products, butyl reclaimed rubber can replace part of chlorobutyl rubber for the production of tire inner liner, which significantly reduces raw material costs.
At present, the inner liner of tires on the market is mostly produced by using chlorinated butyl rubber and natural rubber. Among them, chlorobutyl rubber has extremely low gas permeability, aging resistance, fast vulcanization speed, natural rubber elasticity and high tear strength. Adding an appropriate amount of natural rubber to the inner liner of the tire with chlorobutyl rubber as the main material can significantly improve the elasticity, strength, low temperature performance and tear resistance of the inner liner; but whether it is chlorobutyl rubber or natural rubber They are all high-priced rubber raw materials. Although the airtight layer of tires produced is good in air tightness, high in elasticity and long in service life, but the production cost is too high, it is imperative to mix some low-cost raw materials in the inner liner of tires. .
Butyl reclaimed rubber is a reclaimed rubber made from the price of waste butyl rubber. It retains most of the molecular structure of butyl rubber and has the same performance characteristics as chlorobutyl rubber, but at a price comparable to chlorobutyl rubber and natural. The glue is much lower, so the biggest effect of blending butyl reclaimed rubber in the tire inner liner formulation is to reduce the cost of rubber raw materials; the quality of the butyl reclaimed rubber product is fine, and the partial chlorinated butyl rubber can be replaced by a certain ratio. Reduce the amount of glue and improve the extrusion process of the inner liner of the tire.
However, when butyl reclaimed rubber is blended in the tire innerliner formulation of chlorinated butyl rubber/natural rubber, there are still many problems to be noted: the tire innerliner film produced by chlorobutyl rubber/natural rubber is thinner. The air permeability is relatively large, and a small amount of air blocker may be added after the butyl reclaimed rubber is added to further improve the gas permeability of the inner liner of the tire; and an accelerator such as an accelerator M which can increase the vulcanization rate and shorten the vulcanization time; Anti-aging system; choose sulfur vulcanization and use stearic acid with zinc oxide; use tackifying resin properly; do not use too much butyl reclaimed rubber, replace 1/3 of chlorinated butyl rubber, etc. .
The use of an appropriate amount of butyl reclaimed rubber in the inner liner of the tire produced by using chlorobutyl rubber as the main raw material can reduce the production cost and improve the comprehensive performance of the inner liner; the rubber product manufacturer must select the butyl reclaimed rubber. Be cautious, design chlorinated butyl rubber / natural rubber / butyl reclaimed rubber inner layer formula should be more reasonable mix; in addition, there are many in the process of mastication, mixing, extrusion, molding in the production of tire inner liner Need to pay attention to the problem, Xiaobian will discuss with you later.
Exclusive original article [commercial authorization] reprint, excerpt and excerpt in any form are prohibited without written authorization. Focus on Hongyun rubber: learn the process formula and raw material technology of producing rubber products from recycled rubber to help you reduce costs and increase profits