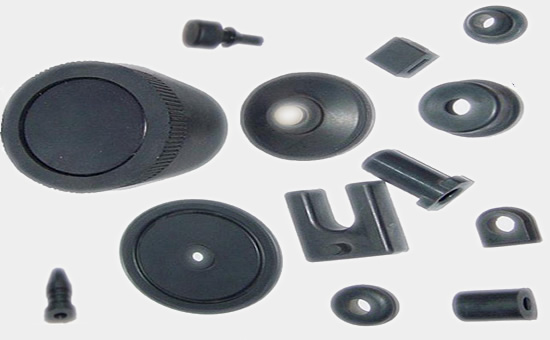
Oil-resistant rubber plug is a rubber plug product used to seal the lid of the container to prevent the leakage and volatilization of engine oil, hydraulic oil, industrial liquid, etc. It needs to have good sealing performance, oil resistance and elasticity, usually using nitrile rubber as the main raw material. In addition to using sub-brand nitrile rubber to reduce raw material costs, nitrile regenerated rubber can also be used. The oil-resistant rubber stopper produced by nitrile reclaimed rubber has excellent oil resistance and sealing performance, and its elasticity is slightly worse than that of nitrile rubber, but it has a huge price and cost advantage. Since nitrile reclaimed rubber is a recycled product, it has a very broad market prospect.
Key points of rubber mixing and vulcanization process for production of oil-resistant rubber plugs from nitrile reclaimed rubber 25E3Y5y:
1. Mix the regenerated nitrile rubber, light calcium carbonate and plasticizer in the internal mixer before adding carbon black to prevent the heat generation after adding carbon black first. roll.
2. Repeatedly chop, squeeze and fold this premix in a mixer to form a highly uniform mass. In this process, various processing aids can be added as needed to improve product performance.
3. Add zinc oxide and accelerator to the mill to make triangular bags of the obtained material, and finally add sulfur, mix evenly and quickly release the tablet.
It is worth noting that: since different nitrile regenerated rubber varieties, sources and processing techniques will affect its mechanical properties and oil resistance, it is necessary to test and adjust according to the actual situation when designing the specific formula.
Recipe for producing oil-resistant rubber plugs from nitrile reclaimed rubber:
Nitrile reclaimed rubber 20kg; light calcium carbonate 15kg; carbon black 1.5kg; dioctyl or dibutyl ester 1.8kg; stearic acid 0.4kg; zinc oxide 0.8kg; M accelerator 0.06kg; DM accelerator 0.08kg; TMTD accelerator 0.025kg; N550 carbon black 0.5kg; sulfur 0.36kg; vulcanization temperature 155-160°C, vulcanization time can be determined according to the size of the product.
Technical considerations for the production of oil-resistant rubber plugs from nitrile reclaimed rubber:
1. As the main raw material, nitrile reclaimed rubber is moderately priced and has excellent mechanical strength, elasticity, oil resistance and high temperature resistance;
2. Light calcium carbonate is used as a filler for oil-resistant rubber plugs to increase hardness and reduce costs;
3. An appropriate amount of carbon black is used for coloring and can also slightly increase the strength of the product; plasticizers are used to improve processing performance;
< /p>
When producing oil-resistant rubber plugs, high-performance nitrile reclaimed rubber should be selected as the main raw material, the rubber mixing process should be strictly controlled, appropriate amount of carbon black, plasticizer, etc. should be added, and scientific formula design and strict process control should be adopted , can produce oil-resistant rubber plugs with favorable price and good quality.
Exclusive original article [commercial authorization] reprint, excerpt and excerpt in any form are prohibited without written authorization. Focus on Hongyun rubber: learn the process formula and raw material technology of producing rubber products from recycled rubber to help you reduce costs and increase profits