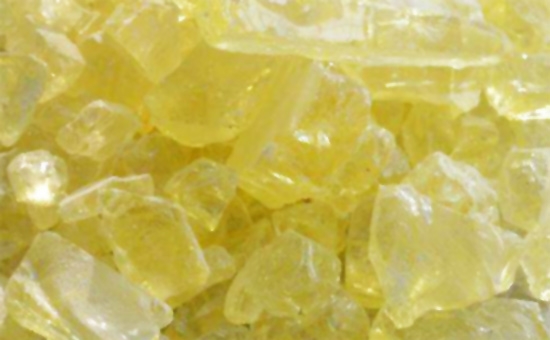
When using nitrile reclaimed rubber to produce cost-effective oil-resistant and wear-resistant rubber products, traditional sulfur vulcanization systems are more common, but there are also nitrile reclaimed rubber products that use resin vulcanization. So why do some nitrile reclaimed rubber products choose resin vulcanization? What is the significance of resin vulcanized nitrile rubber? How to design the resin vulcanization system for nitrile reclaimed rubber products? The editor will discuss with you one by one today.
1. The reason why nitrile reclaimed rubber is cured by resin
Nitrile reclaimed rubber can be used to produce various oil-resistant and wear-resistant rubber products such as oil seals, wear-resistant rubber pads, etc. These rubber products will continue to generate heat during the working process. The nitrile reclaimed rubber vulcanized with resin has excellent resistance Thermal aging performance. Therefore, nitrile reclaimed rubber products that have strict requirements on heat resistance are more willing to choose resin vulcanization to ensure the heat resistance of the finished product and extend the service life of nitrile reclaimed rubber products.
2. The vulcanization mechanism of resin vulcanized nitrile reclaimed rubber
When resin vulcanizes nitrile reclaimed rubber, the active functional groups can interact with the active groups in the macromolecules in the nitrile reclaimed rubber during the vulcanization process. The resin 2LLYY1016 molecules form the cross-linking structure between the macromolecules to achieve a good The vulcanization effect. The vulcanizing agent commonly used in nitrile reclaimed rubber resin vulcanization system is alkyl phenolic resin. Compared with other curing systems, the vulcanization speed of nitrile reclaimed rubber vulcanized with resin is slower.
3. Design skills of nitrile reclaimed rubber resin curing system
When nitrile reclaimed rubber is vulcanized with resin, rational use of resin can further improve the comprehensive index of nitrile reclaimed rubber products. In actual production, resins with too large molecular weight should not be used for vulcanization of nitrile reclaimed rubber, in order to avoid vulcanizing agents from affecting the crosslinking effect and physical properties of nitrile reclaimed rubber. A proper amount of 1-5 parts of polyisocyanate, polyol and other polyfunctional compounds can increase the crosslinking density of nitrile vulcanizates. When alkyl phenolic resin is used to vulcanize nitrile reclaimed rubber, the amount of vulcanizing agent is generally controlled between 30-40 parts, the vulcanization temperature is controlled between 150-160℃, and the vulcanization time is controlled at about 2 hours.
When the nitrile reclaimed rubber is vulcanized with resin, the amount of resin is too much, and the excess resin cannot undergo a vulcanization reaction with the nitrile reclaimed rubber, only plasticizing. This part of the resin that can only play a role in plasticizing will reduce the tensile strength of the nitrile reclaimed rubber and increase the permanent deformation of the reclaimed rubber vulcanizate. The amount of resin must be controlled reasonably. Properly prolonging the vulcanization time or increasing the vulcanization temperature can further improve the vulcanization efficiency of nitrile reclaimed rubber. Later editors will continue to share with you other issues about the use of resin vulcanization of nitrile reclaimed rubber.
Exclusive original article [commercial authorization] reprint, excerpt and excerpt in any form are prohibited without written authorization. Focus on Hongyun rubber: learn the process formula and raw material technology of producing rubber products from recycled rubber to help you reduce costs and increase profits