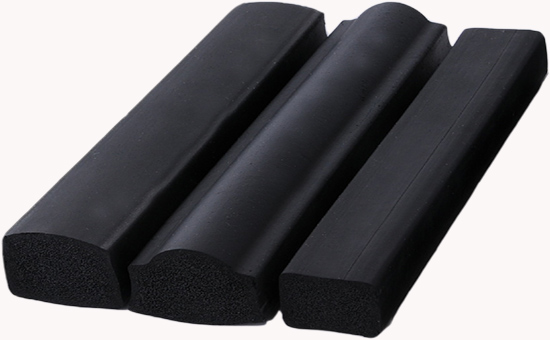
When using EPDM reclaimed rubber to produce rubber products with high requirements for softness and cushioning effect, it is generally required to use rubber with a Sauer hardness of less than 55, which is generally achieved by increasing the amount of softener. However, in actual production, there are many problems when preparing low-hardness EPDM reclaimed rubber compound by using a large number of softeners; Reasonable design of EPDM reclaimed rubber product formula can not only meet the demand for low hardness of products, but also reduce the cost of raw materials and improve the processing technology performance of rubber compounds.
1. EPDM reclaimed rubber is prone to the following 7 problems when preparing low-hardness rubber by filling a large amount of softener.
(1) The strength of the rubber material is low, and the physical and mechanical properties are poor;
(2) Slippage may occur when a large amount of oil is added during mixing, and the low viscosity of the rubber material reduces the shear stress during mixing, and the filler particles are difficult to disperse, which affects the dispersion of the rubber material and the appearance quality of the extruded product;
(3) The strength of the rubber compound is low, the feeding material is not smooth during extrusion, it is easy to return to the glue, and the stiffness and dimensional stability of the product are poor;
(4) The low pressure of the extruder head makes it difficult to discharge the gas, the vacuum effect of the vacuum area is poor, and pores are easy to form in the product during atmospheric pressure vulcanization, especially in the large-section products;
(5) The strength of the rubber compound is low, the traction performance is poor, especially in the high filling formula, it is more likely to cause profile breakage or traction deformation;
(6) The low pressure in the mold cavity during molding vulcanization makes it difficult to discharge the gas, which affects the density of the product and is prone to gas entrapment or defects;
(7) A large number of softeners reduce the efficiency of vulcanization, and the surface of the product is prone to stickiness.
2. In actual production, rubber products manufacturers can prepare low-hardness rubber materials that meet the requirements in the following ways.
(1) When EPDM reclaimed rubber and EPDM rubber are used together to produce low-hardness rubber products, it is recommended to choose EPDM reclaimed rubber with low hardness, and use it together with EPDM rubber filled with oil in the polymerization stage to ensure the necessary processing technology performance of the rubber compound. The high molecular weight and high ethylene content of EPDM oil-filled glue can make it obtain high rubber strength even if low reinforcing filler is used, reduce the problem caused by adding a large amount of oil to the compounding agent, shorten the mixing time, and improve the strength, stiffness and traction resistance of the rubber compound.
(2) Medium or low reinforcing carbon black (except for rubber compounds with special requirements for tensile strength, tear resistance, wear resistance, etc.) is usually used when EPDM reclaimed rubber is prepared with low hardness, which has better dispersion in the rubber compound. Due to the small shear force of low-viscosity rubber mixing, the filler is easy to agglomerate or easy to have poor dispersion, so it is recommended to use a lower mixing temperature, and appropriately extend the mixing time or increase the number of thin passes to improve the dispersion.
(3) Choose a filler oil with good compatibility with EPDM reclaimed rubber, which can effectively prevent the exudation of oil, and the commonly used ones are paraffin oil, naphthenic oil, aromatic oil, mechanical oil, etc. In addition, although the softening effect of vulcanized paste in low-hardness rubber compound is poor, it can significantly improve the stiffness of rubber and prevent porosity in products, so vulcanized paste can also be used appropriately in low-hardness rubber softening system when necessary.
(4) Adding a large amount of low-molecular-weight softener will reduce the cross-linking efficiency of the rubber compound, and at the same time dilute the vulcanizing agent, so the vulcanization system in the rubber compound formulation of low-hardness EPDM reclaimed rubber 2SLYY1116 needs to be appropriately enhanced, especially the rubber compound using peroxide vulcanization. In actual production, a large number of low-molecular-weight softeners will compete with macromolecules for active free radicals in EPDM reclaimed rubber using peroxide vulcanization, affecting the cross-linking efficiency, so the amount of peroxide in low-hardness rubber should be increased, and softeners such as naphthenic oil or aromatic oil that have a greater impact on peroxide vulcanization should not be used.
When using EPDM reclaimed rubber as the main raw material to prepare low-hardness rubber compounds, rubber product manufacturers also need to appropriately adjust the production process conditions, especially the mixing and vulcanization process parameters, and continue to discuss related issues with you in the future.
Exclusive original article [commercial authorization] reprint, excerpt and excerpt in any form are prohibited without written authorization. Focus on Hongyun rubber: learn the process formula and raw material technology of producing rubber products from recycled rubber to help you reduce costs and increase profits