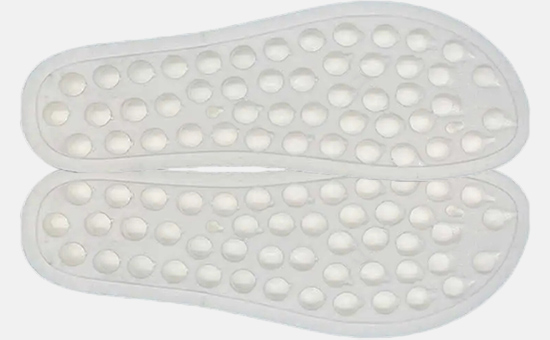
PU polyurethane is a polymer material with excellent mechanical properties and strong plasticity, which is used to manufacture shoe sole glue with soft texture, low density, good dimensional stability, wear resistance, flexural resistance and other performance characteristics. However, the price of PU materials is high, so many sole manufacturers want to mix some low-cost raw materials, and rubber powder is one of the more ideal choices. So can rubber powder be applied to PU soles? Which rubber powder is more suitable?
1. Classification of rubber powder
Rubber powder, waste tires, rubber products or other rubber materials processed into powdered materials by mechanical crushing, chemical treatment or microwave treatment can be divided into ordinary rubber powder, activated rubber powder and modified rubber powder according to whether the surface is modified. Activated rubber powders 2SLYY1027 generally refer to the chemical treatment of rubber powders to enhance their surface activity, thereby improving adhesion to new rubber or other materials.
After the surface of the rubber powder is treated by chemical or physical methods, the compatibility and adhesion of the rubber powder to the matrix material are better. When using PU materials to manufacture shoe soles, activated rubber powder that has been modified by the surface is generally used.
2. The advantages of PU sole glue mixed with activated rubber powder
PU soles have the characteristics of lightness, comfort, good elasticity, wear resistance, and easy processing, but they are costly, have poor air permeability, are easy to absorb water, and have poor grip on slippery surfaces. The addition of some surface-modified activated rubber powder to PU sole glue can not only reduce the material cost, but also improve the tensile strength, tear strength, elasticity and wet friction factor of the sole glue, and improve the durability and safety of PU soles.
3. The skill of PU sole glue mixed with activated rubber powder
In actual production, about 20 parts of activated rubber powder are mixed with PU sole glue, and the mechanical properties of the rubber compound are basically unchanged; The addition of 10-25 parts of surface modified rubber particles can increase its wet friction factor by 20%.
In actual production, rubber powder can not only be used in the sole rubber based on PU materials, but also more mixed in the rubber outsole, midsole, heel and other parts; When mixing rubber powder with rubber powder processed from different materials to reduce costs and improve performance, we must fully consider factors such as the particle size, surface treatment, and compatibility with the matrix material to ensure that the performance of the final product meets the design requirements and reduce more costs on the premise of ensuring product quality.
Exclusive original article [commercial authorization] reprint, excerpt and excerpt in any form are prohibited without written authorization. Focus on Hongyun rubber: learn the process formula and raw material technology of producing rubber products from recycled rubber to help you reduce costs and increase profits