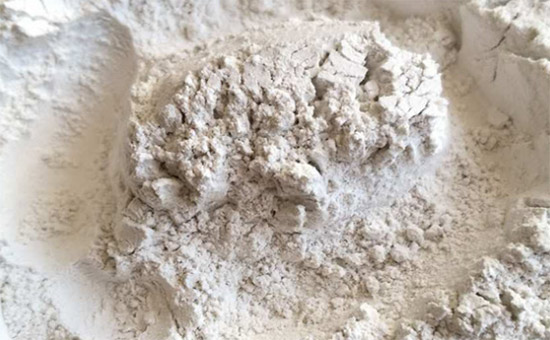
Rubber filler can reduce the cost of raw materials in the processing of rubber products, and can also improve the processing technology of rubber products, improve the tensile strength, elongation at break, wear resistance, etc., which is the most used in rubber products except rubber raw materials. The compounding agent; therefore, the quality of the rubber filler has a great influence on the quality of the rubber product. The fineness is one of the important indexes for the rubber manufacturers to select the filler. So the finer the rubber filler, the better?
Rubber fillers can be divided into reinforcing fillers and non-reinforcing fillers according to the reinforcing properties. Generally, the reinforcing fillers such as carbon black have higher fineness and larger specific surface area, and the contact area with rubber is relatively larger. The better the reinforcing performance in the medium; the higher the fineness of the non-reinforcing filler such as light calcium, the better the mixing effect in the rubber.
However, from another point of view, non-reinforcing fillers, even if the fineness is sufficient, but uneven dispersion will affect the compounding effect of the rubber compound. The rubber filler is mostly powder. In terms of surface properties, after the powder rubber filler is mixed into the rubber, the particles are surrounded by the rubber molecules, and the rubber surface of the particle is wetted by the rubber. The rubber filler has better reinforcing performance in the rubber compound. The filler particles which are not easily wetted by the rubber are easy to agglomerate in the rubber compound and are not easily dispersed, which directly affects the reinforcing property.
Therefore, the role of the rubber filler in the rubber is also related to its surface properties, and the higher the fineness of the rubber filler, the better the reinforcing performance. In the production of rubber products, the type, structure and surface properties of the rubber fillers will affect the performance of the rubber products. Therefore, the manufacturers can judge the quality of the rubber fillers by the single size.
When using rubber or recycled rubber to produce rubber products, it is necessary to select the appropriate type of rubber filler according to the color and index of the rubber products. For products with high gloss requirements on the surface of rubber products, it is necessary to select high-fine rubber fillers and extruded rubber. When selecting the filler, the product should ensure that the product can be smoothly extruded: light-colored rubber products and colored rubber products need to choose white, light-colored rubber fillers such as white carbon black and clay, and use as much reinforcement as possible for high-strength and high-wear rubber products. Reinforcing filler with good performance and good wear resistance such as high wear-resistant carbon black.
For rubber fillers such as calcium carbonate which are not easily wetted by rubber and difficult to disperse in the rubber compound, an appropriate amount of stearic acid may be added to reduce the surface tension of the filler, increase the degree of wetting, and improve the reinforcing effect. In short, starting from the actual situation, consider the problem in many aspects, choose the most suitable rubber filler for your own rubber products, and design the most reasonable reinforcement filling system.
Exclusive original article [commercial authorization] reprint, excerpt and excerpt in any form are prohibited without written authorization. Focus on Hongyun rubber: learn the process formula and raw material technology of producing rubber products from recycled rubber to help you reduce costs and increase profits