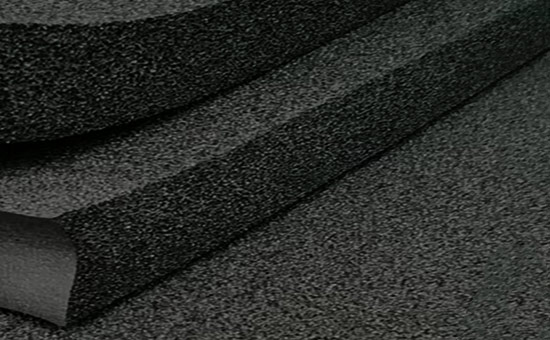
Sponge rubber has the characteristics of good elasticity, light texture, low density, good cushioning performance, thermal insulation, sound insulation, etc., and has a wide range of applications in various fields. Recycled rubber can be used alone or in combination with suitable varieties of raw rubber (latex recycled rubber and natural rubber, EPDM recycled rubber combined with EPDM rubber, nitrile recycled rubber and nitrile rubber, etc.) to prepare various sponge foam rubber products, effectively reducing the cost of raw materials. When using recycled rubber to produce sponge foam rubber products, the choice of blowing agent is crucial.
When choosing a foaming agent for recycled rubber sponge foam rubber products, you need to focus on the following issues.
1. Consider the processing technology and processing temperature of recycled rubber sponge foam rubber products
The temperature of the compound of the refiner is generally below 80 °C, the temperature of the compound of the mixer is below 130 °C, and the vulcanization temperature is generally among 130 °C and 200 °C, so it is recommended to choose a foaming agent with a decomposition temperature in the range of 140 °C-180 °C, and the dosage is generally 2-8 parts. In order to adapt the decomposition temperature of the blowing agent to the vulcanization conditions, it is recommended to use two or more varieties of blowing agent together, or add a blowing agent.
2. Consider the influence of foaming auxiliaries and other compounding agents on the decomposition of foaming agents
In actual production, the decomposition of chemical blowing agents by some compounds in foaming additives and recycled rubber sponge foam rubber products can be divided into two aspects: acceleration and inhibition. For example E5LYY35 stearic acid and zinc oxide can accelerate the decomposition of DPT. When stearic acid and DPT coexisted, the acceleration effect of zinc oxide was extremely significant at the beginning of the reaction, but the acceleration effect gradually disappeared with the prolongation of time, and even showed an inhibitory effect.
When using recycled rubber to produce sponge foam rubber products, the decomposition temperature range of the blowing agent in the rubber material tends to widen and decrease, such as the blowing agent decomposed at 150°C, which may decompose at 140~150°C or 130~150°C after being added to the compound; Foaming at a decomposition temperature lower than that of the blowing agent will cause problems such as unstable gas generation, undecomposed color pollution, pungent odor, or corrosion of the mold.
3. Consider the decomposition rate of the blowing agent
The decomposition speed of the blowing agent refers to the time from the beginning of the decomposition of the blowing agent to the end of the decomposition. Therefore, it is recommended to use a blowing agent with a slow decomposition rate in the production of recycled rubber sponge foam rubber products.
4. Consider the heat release when the blowing agent decomposes
Different varieties of blowing agents have different heat release during decomposition, and the heat release of DPT is the largest when the blowing agent is decomposed, and the blowing agents AC, TSH and OBSH are less than 50% of it. In the production of recycled rubber sponge foam rubber products, it is recommended to use a blowing agent with low release heat to avoid discoloration and degradation caused by heat generation inside the material when the amount of blowing agent is too high. When using recycled rubber to produce thick-walled sponge rubber, the heat of decomposition of the blowing agent is beneficial to compensate for the lack of sulfur in the deep layers inside.
5. Consider the amount of air generated by the blowing agent
In actual production, the gas generation of blowing agent is generally among 100-150mL/g, generally 60% when using the two-stage foaming process, and less than 50% when using the first-stage foaming process and pressure-free foaming process. When the blowing agent releases non-nitrogen, the efficiency is lower due to the large post-shrinkage rate. When using recycled rubber to prepare spongy bodies with small pores, the order of different types of blowing agents from easy to difficult is as follows: AC>OBSH>TSH>DPT.
It should be noted that the pores of recycled rubber sponge foam rubber products are also related to processing methods, vulcanization conditions, formula design and other factors, under reasonable conditions, the use of DPT foamed recycled rubber can also produce sponge foam rubber products with smaller pores than AC.
When choosing a blowing agent for recycled rubber sponge foam rubber products, it is also necessary to consider the toxicity of the blowing agent, not only the toxicity of the product itself, but also whether the decomposed product is toxic, such as AZDN (azo isobutyronitrile) and other blowing agents are toxic, and formaldehyde is produced when DPT decomposes. What are the commonly used blowing agents in the production of recycled rubber sponge foam rubber products? We will discuss this with you later.
Exclusive original article [commercial authorization] reprint, excerpt and excerpt in any form are prohibited without written authorization. Focus on Hongyun rubber: learn the process formula and raw material technology of producing rubber products from recycled rubber to help you reduce costs and increase profits