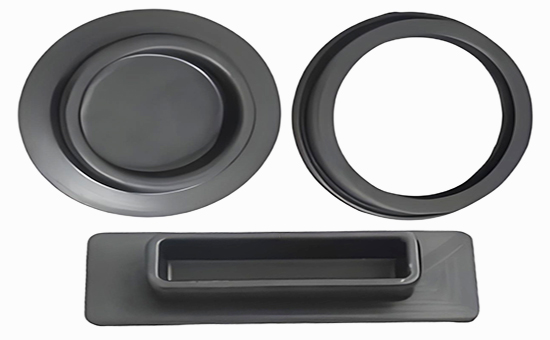
Rubber molded products are rubber products processed by mold forming process, and specific shape and dimensional accuracy are obtained after vulcanization and shaping in the mold cavity. As a high-priced raw material for raw rubber replacement, reclaimed rubber can be used alone or combined with natural rubber and synthetic rubber to produce rubber molded products, reducing the cost of raw rubber and production energy consumption. When using reclaimed rubber to produce model rubber products, it includes five main processes: batching, rubber compound manufacturing, semi-finished product manufacturing, vulcanization and trimming.
1. Production process of recycled rubber molded products - ingredients and precautions
When using reclaimed rubber as the main raw material to produce model rubber products, the batching process involves a variety of raw materials.
First of all, it is necessary to test the appearance, physical properties (tensile strength, wear resistance) and chemical properties (oil resistance, heat resistance) of rubber raw materials (reclaimed rubber or natural rubber and synthetic rubber) and rubber additives (vulcanizing agents, accelerators, reinforcing agents, fillers, etc.) to ensure that they meet the process requirements; Fillers (such as carbon black, silica) are dried and ground to remove moisture and improve fineness, so as to avoid affecting the uniformity of rubber dispersion.
The compounding agent used in recycled rubber moldings is classified, and the rubber and compounding agent are accurately weighed and reviewed according to the formula ratio to avoid the instability of product performance caused by errors; Adjust the feeding sequence according to the characteristics of the compound (e.g. carbon black post-addition can avoid scorching) to ensure homogeneity of mixing and processability.
2. Production process of recycled rubber molded products - rubber compound manufacturing and precautions
Recycled rubber molded products require uniform dispersion, stable performance and high process performance of rubber compounds, and some high-precision recycled rubber products need to be filtered. In the process of making rubber E4LYY919 compounds, it is necessary to strictly control the mixing temperature and time to avoid scorching caused by excessive mixing temperature, and to ensure that the rubber compound and compounding agent are fully mixed. Generally, the temperature of the internal mixer is controlled among 120-150°C, and the roll temperature of the open mixer is adjusted according to the characteristics of the reclaimed rubber. The internal mixer applies appropriate vulcanization pressure to promote dispersion.
3. Production process of recycled rubber molded products - semi-finished product manufacturing and precautions
Recycled rubber molded products adopt the general molding vulcanization method, which requires the unit consumption (shape and quality) of the manufactured semi-finished products to be accurate, so that the mold installation speed is fast, and the rubber edge of the vulcanized products is thin. It is recommended to manufacture with precision preforming equipment whenever possible. For reclaimed rubber products using injection molding vulcanization method, it is necessary to make the rubber material have good fluidity. The use of reclaimed rubber to produce composite rubber seals with embedded skeletons requires surface treatment of various skeleton materials, including the selection of suitable adhesives for coating.
4. Production process of recycled rubber molded products - vulcanization and precautions
The vulcanization of recycled rubber molds adopts high temperature short-time, multi-mold cavity, large plate mold and tearing edge mold, which can improve production efficiency and then improve economic benefits. During vulcanization, it is necessary to set the vulcanization temperature reasonably according to the type of reclaimed rubber and original rubber (about 150 °C for nitrile rubber and about 160 °C for EPDM rubber), and control the vulcanization time (about 40min) and pressure (5-20MPa); Ensure that the parallelism of the mold and the position of the exhaust hole are reasonable to avoid product delamination or lack of glue; The parting surface needs to be chamfered and polished to reduce the risk of tearing the mold.
5. Production process of recycled rubber molded products - trimming and precautions
Mechanized and semi-automated edge removal and assembly are used to ensure the accuracy and dimensional tolerances of recycled rubber moldings.
When using reclaimed rubber to produce model rubber products, it is also necessary to pay attention to the following points: Clean the mold in time after vulcanization to avoid the residual rubber material affecting the next production; Pay attention to protection during high-temperature mixing to avoid scalding; Internal mixers, open mixers and other equipment need to be regularly maintained to ensure operational safety. In the production process of recycled rubber molded products, strict control of the production process can effectively improve the dimensional accuracy, physical properties and production efficiency of the products, reduce the scrap rate, and improve economic benefits.
Exclusive original article [commercial authorization] reprint, excerpt and excerpt in any form are prohibited without written authorization. Focus on Hongyun rubber: learn the process formula and raw material technology of producing rubber products from recycled rubber to help you reduce costs and increase profits