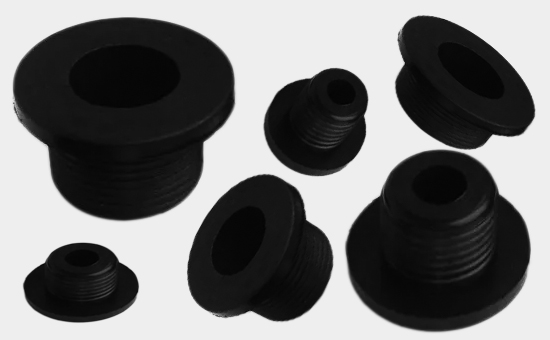
EPDM reclaimed rubber has the basic performance characteristics of EPDM rubber, and can be used alone or in combination with EPDM raw rubber to produce various rubber products, effectively reducing the cost of raw materials. In actual production, proper design of the formulation components of EPDM reclaimed rubber products can further optimize product quality while reducing costs. This time, the editor will focus on sharing with you the vulcanization components of EPDM reclaimed rubber, reinforcing filling Component, plasticizing component, anti-aging component and tackifier component design.
1. Vulcanization components of EPDM reclaimed rubber
When using EPDM reclaimed rubber to produce rubber products, you can choose sulfur vulcanization, organic peroxide vulcanization, quinone oxime vulcanization and resin vulcanization.
EPDM reclaimed rubber adopts sulfur vulcanization, which has the characteristics of good vulcanizate comprehensive performance, simple vulcanization process and low cost. Common combinations: sulfur-accelerator M/TMTD, sulfur-accelerator M/TMTD/TDD/DPTT, sulfur- Curing agent DTDM-accelerator TMTD/ZDBC/EZ etc. EPDM reclaimed rubber peroxide vulcanizate has the characteristics of good aging resistance, small compression set, flat plate and steam vulcanization without blooming, and DCP vulcanization is commonly used. The resin vulcanization system vulcanizes EPDM reclaimed rubber with slow vulcanization speed, good heat aging resistance and high temperature performance, and brominated alkyl phenolic resin is commonly used.
2. Reinforcing and filling components of EPDM reclaimed rubber
When using EPDM reclaimed rubber to produce rubber products, reinforcing fillers can give the rubber compound better mechanical strength. Commonly used reinforcing agents are carbon black and white carbon black. Commonly used fillers are calcium carbonate, talc and clay etc.
In actual production, when EPDM reclaimed rubber is reinforced with carbon black, fine particle furnace black (better wear resistance) and groove black are commonly used, and acetylene carbon black and conductive furnace black can be used in the production of conductive rubber products. The reinforcing effect of silica is similar to that of carbon black, which can give the EPDM reclaimed rubber better adhesion, especially the adhesion among metals and fibers; it should be noted that the peroxide-cured ternary When ethylene-propylene reclaimed rubber is reinforced with silica, it is necessary to adjust the PH value of the rubber compound. 2-4 parts of ethylene glycol are commonly used to avoid the reaction of peroxide and silica to produce harmful substances.
Calcium carbonate is a commonly used filler for EPDM reclaimed rubber products, among which light calcium and activated calcium carbonate have a certain reinforcing effect in EPDM reclaimed rubber. Talc powder can be used together with carbon black to improve the dispersion degree of carbon black in EPDM reclaimed rubber 2ELYY622, especially suitable for heat resistance, acid resistance, alkali resistance and electrical insulation EPDM reclaimed rubber products. When using EPDM reclaimed rubber to produce extruded rubber products, an appropriate amount of clay is filled, and the combination of clay and carbon black can further improve the extrusion performance of the rubber compound.
The important components of EPDM reclaimed rubber are plasticizing components, anti-aging components and tackifier components. Tomorrow, Xiaobian will continue to share related issues with you.
Exclusive original article [commercial authorization] reprint, excerpt and excerpt in any form are prohibited without written authorization. Focus on Hongyun rubber: learn the process formula and raw material technology of producing rubber products from recycled rubber to help you reduce costs and increase profits