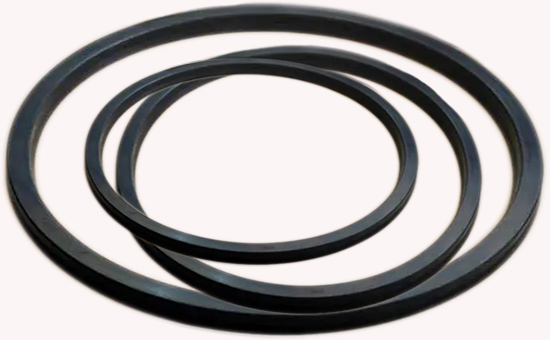
Rubber additives are an indispensable part of the formulation of EPDM/reclaimed rubber products. Reasonable selection of additives can not only improve the process performance of the rubber compound, improve the comprehensive index of the product, but also effectively reduce the cost. In actual production, when EPDM rubber and EPDM reclaimed rubber are used together to produce rubber products, the mixing process is mostly carried out in an internal mixer, and the variety and amount of rubber additives directly affect the performance of EPDM rubber/reclaimed rubber. Mixing process in an internal mixer.
1. The compounding agent of the vulcanization system affects the mixing of EPDM rubber/reclaimed rubber in the internal mixer
When using EPDM rubber/EPDM reclaimed rubber and rubber to produce rubber products, the vulcanization system directly determines whether the mixed rubber is mixed in one stage or two stages, and whether the mixing temperature and mixing time are determined. 2ELYY530 and other processes parameter key. When EPDM rubber/reclaimed rubber is mixed in an internal mixer, the temperature of adding the vulcanizing agent should be lower than the safe operating temperature. In actual production, the safe operation temperature of sulfur and accelerator is about 110℃, the safe operation temperature of peroxide DCP (dicumyl peroxide) is 120℃, and the safe operation temperature of dicumyl tert-butyl peroxide The temperature is about 130°C.
2. The compounding agent of the reinforcement system affects the mixing of EPDM rubber/reclaimed rubber in the internal mixer
EPDM/reclaimed rubber is generally reinforced with carbon black. Among them, high-structure fine-particle carbon black such as high-wear carbon black is difficult to disperse in EPDM compounds, and heat generation is large during mixing; low-structure coarse-grain carbon black such as carbon black and semi-reinforced carbon black is quickly extruded. The EPDM compound is easy to disperse, has a larger filling amount and less heat generation. In theory, the larger the specific surface area of carbon black, the longer the mixing time, the shorter the scorching time, and the worse the mixing operability; the higher the carbon black structure, the longer the mixing time, the shorter the scorching time, and the little change in the mixing operability. ; The more the amount of carbon black, the longer the time required for mixing, the shorter the scorch time, and the poorer mixing operability.
Appropriate addition of white inorganic fillers such as calcium carbonate, clay, talc and other white inorganic fillers to the EPDM original rubber/reclaimed rubber compound can reduce costs and improve the mixing performance of the rubber compound in an internal mixer. Using fine particle fillers or white inorganic fillers treated with surface activity, the physical and mechanical properties of EPDM rubber/reclaimed rubber vulcanizates are better.
3. Rubber oil affects the mixing of EPDM rubber/reclaimed rubber in an internal mixer
When using EPDM rubber/reclaimed rubber to produce rubber products, it is beneficial to select the appropriate rubber operating oil for the mixing of the rubber in the internal mixer. For example, commonly used paraffin oil, naphthenic oil, aromatic oil, etc., have good compatibility with EPDM rubber and EPDM reclaimed rubber. In general, the larger the amount of filler in EPDM/reclaimed rubber products, the larger the amount of operating oil.
In actual production, when using rubber oil to improve the mixing performance of EPDM rubber/reclaimed rubber compound in an internal mixer, it is necessary to control the amount of rubber oil, pay attention to the compatibility among oil and rubber, and due to Insufficient shear force and slow temperature rise during mixing lead to the problem of the quality of the mixed rubber being reduced.
4. Processing aids affect the mixing of EPDM rubber/reclaimed rubber in an internal mixer
When EPDM rubber and EPDM reclaimed rubber are used to produce rubber products, appropriate use of dispersing aids, flow aids, lubrication aids, active agents, tackifiers, polar additives and other functional additives can improve EPDM adhesives. The mixing operation of the material in the internal mixer should not be too large, so as to avoid these processing aids becoming incompatible substances during mixing and causing problems such as frosting on the surface of the product.
When mixing EPDM reclaimed rubber or EPDM rubber/reclaimed rubber in an internal mixer, you must choose the compounding agent carefully to improve the mixing performance of the rubber compound; the editor will continue to communicate with you later. Discuss related issues.
Exclusive original article [commercial authorization] reprint, excerpt and excerpt in any form are prohibited without written authorization. Focus on Hongyun rubber: learn the process formula and raw material technology of producing rubber products from recycled rubber to help you reduce costs and increase profits