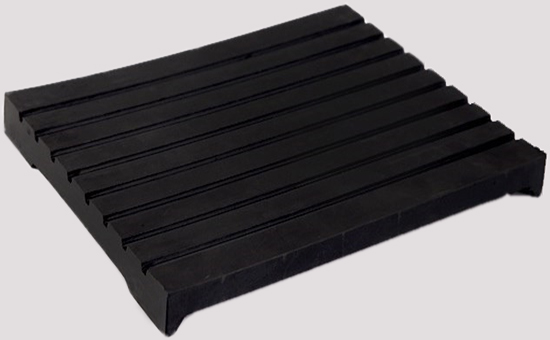
EPDM rubber and EPDM reclaimed rubber have excellent heat resistance, weather resistance, aging resistance, good damping performance, and dynamic performance. They can be used to produce automobile engine bearings, bridge bearings and other shock-absorbing products. Among them, the use of reclaimed rubber in an appropriate amount can effectively reduce the cost of raw materials. In actual production, when using EPDM virgin rubber or reclaimed rubber to produce shock-absorbing rubber products, the type and amount of reinforcing agent directly affect the damping performance of EPDM vulcanizate.
1. Reinforcing agent and damping performance of EPDM vulcanizate
In actual production, the EPDM compound can only obtain the corresponding strength and wear resistance by adding enough reinforcing agent. In principle, the addition of a reinforcing agent will increase the internal friction the rubber macromolecular segment and the reinforcing particles or the reinforcing particles and the reinforcing particles, and the damping performance of the vulcanizate will increase. Generally, the greater the filling amount of the reinforcing agent, the greater the hysteresis of the EPDM vulcanizate and the better the damping performance. At the same time, the dynamic magnification (dynamic elastic modulus/static elastic modulus) and dynamic heat generation increase accordingly.
2. Selection skills of carbon black for EPDM shock-absorbing material
Carbon black is the most commonly used reinforcing filler in the production of rubber products. In actual production, improving the reinforcing performance of carbon black has a similar effect to increasing the filling amount. When using EPDM rubber or EPDM reclaimed rubber 2YLYY830 to prepare shock-absorbing rubber, use some medium reinforcing carbon blacks, such as N500, N774, etc., on the premise that the strength meets the requirements of the product, and the vulcanized rubber can obtain good dynamics Performance: In the production of high-damping EPDM shock-absorbing materials, a large amount of high-reinforcing carbon black such as N330 is required.
3. The role of white carbon black in EPDM damping materials
Silica has the effect of dispersing and delaying vulcanization in rubber. Therefore, in the production of EPDM shock-absorbing compound, white carbon black is generally not used alone as the main reinforcing agent. In actual production, the addition of white carbon black to the EPDM compound reinforced with carbon black can further improve the fatigue resistance and tear resistance of the vulcanizate,etc.
4. Selection skills of inorganic fillers for EPDM shock-absorbing materials
Inorganic fillers can reduce the cost of raw rubber by increasing the volume of the product in the production of rubber products. In actual production, adding a small amount of inorganic filler to the EPDM compound has little effect on the damping performance and stiffness of the vulcanizate.
When using EPDM rubber, EPDM reclaimed rubber or EPDM rubber/reclaimed rubber combined with rubber to prepare EPDM shock-absorbing rubber products, rubber product manufacturers need to choose suitable reinforcing fillers according to actual needs, and ensure that the products are other The damping performance of EPDM vulcanizate is further improved while the physical and mechanical properties. Later editors will continue to discuss related issues with you.
Exclusive original article [commercial authorization] reprint, excerpt and excerpt in any form are prohibited without written authorization. Focus on Hongyun rubber: learn the process formula and raw material technology of producing rubber products from recycled rubber to help you reduce costs and increase profits