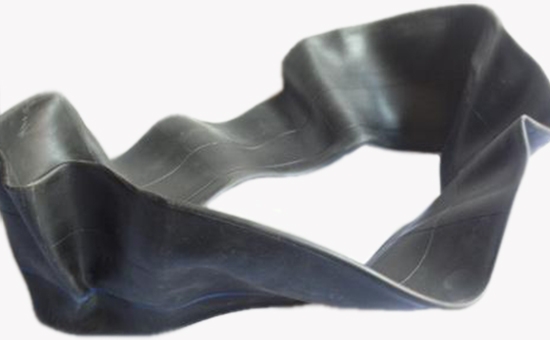
Butyl reclaimed rubber has excellent air tightness and can replace butyl rubber to produce inner tube products, effectively reducing raw material costs. In actual production, some butyl inner tube manufacturers combine butyl reclaimed rubber with a small amount of natural rubber in a certain proportion to produce inner tube products with better overall performance. So what is the significance of using natural rubber in the butyl reclaimed rubber inner tube? What problems should be paid attention to when using butyl reclaimed rubber/natural rubber to produce inner tubes?
1. The significance of the combined use of butyl reclaimed rubber/natural rubber
Butyl reclaimed rubber has good air tightness, heat resistance, ozone resistance and aging resistance, and retains the basic performance characteristics of butyl rubber. Compared with butyl virgin rubber, butyl reclaimed rubber has a faster vulcanization speed and has better effect when used with other types of rubber 2LLYY1127; the disadvantage is that the mechanical strength is slightly lower than that of butyl virgin rubber. Natural rubber has high mechanical strength and good elasticity. The inner tube product produced by combining butyl reclaimed rubber with a small amount of natural rubber has good air tightness, low cost, good elasticity, suitable mechanical strength and longer service life.
2. Formula design of butyl reclaimed rubber/natural rubber inner tube
When using butyl reclaimed rubber and a small amount of natural rubber to produce rubber innertubes, the performance of innertubes produced when the ratio of butyl reclaimed rubber/natural rubber is 80/20 is more stable. In the production of butyl innertubes with butyl/natural rubber, traditional sulfur vulcanization systems can be selected, together with zinc oxide, stearic acid, etc. The reinforcement system uses general carbon black such as N660, which has high tensile stress, good elasticity, and excellent processing performance. The dosage is controlled between 30-40 parts; or high wear-resistant carbon black, semi-reinforcing carbon black, and fast pressing Black and use. Choose paraffin oil as a softener, with a small amount of tackifying resin.
3. Process conditions of butyl reclaimed rubber/natural rubber inner tube
When butyl reclaimed rubber/natural rubber is used to produce inner tube products, the mixing process is generally carried out in an internal mixer. During mixing, the mixing pressure is controlled at about 0.4-0.6 Pa, and the mixing temperature is controlled at 135-140℃. After fully mixing, filter in the filter, press out in the extruder, fix the length, stick the nozzle, and connect in the splicing machine; during vulcanization, control the vulcanization temperature at about 150°C to fully vulcanize.
In actual production, the combined ratio of butyl reclaimed rubber and natural rubber can be determined according to actual needs. Under the premise that the total amount of raw rubber is 100 parts, the amount of butyl reclaimed rubber is generally controlled at 60-80 parts, and the amount of natural rubber is controlled at 20-40 copies. Then, according to the specific needs of the butyl inner tube, the appropriate variety of compounding agents and additives are selected, and the production process parameters are appropriately adjusted to meet the performance requirements of the rubber inner tube while reducing more raw material costs.
Exclusive original article [commercial authorization] reprint, excerpt and excerpt in any form are prohibited without written authorization. Focus on Hongyun rubber: learn the process formula and raw material technology of producing rubber products from recycled rubber to help you reduce costs and increase profits