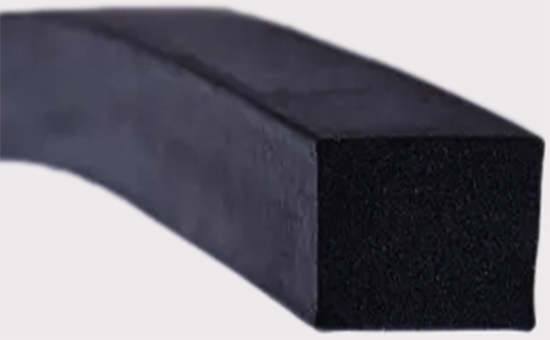
EPDM reclaimed rubber has excellent performance characteristics such as high and low temperature resistance and aging resistance. It can be used alone or in combination with EPDM original rubber to produce rubber products, effectively reducing the production cost of EPDM products. When using EPDM reclaimed rubber to produce rubber products, the mixing process is mostly carried out in an internal mixer to better ensure the uniformity of mixing. The amount of rubber loaded directly affects the mixing effect of the reclaimed rubber in the internal mixer.
The amount of glue loaded is the filling coefficient and the amount of material. When the EPDM reclaimed rubber is mixed in the internal mixer, the amount of material must be appropriate at one time. Too much or too little material will make the dispersion and uniformity worse, and the production efficiency will be reduced. .
In actual production, the feeding amount of EPDM reclaimed rubber is too large, and the material has no room for turning and turning. smelting, the uniformity of the rubber compound is reduced. On the contrary, when the amount of EPDM reclaimed rubber is insufficient in the internal mixer, it will reduce the pressure exerted by the top bolt on the rubber material, so the rubber material cannot obtain the necessary shearing effect and kneading effect, and even cause Slippage and idling, prolonging the mixing time, can not get a uniform quality of the mixed rubber.
The feeding amount of EPDM reclaimed rubber in the internal mixer depends on the formula components, the Mooney viscosity and hardness of the rubber compound, and the wear and tear of the internal mixer. The theoretical calculation formula of the one-time feeding amount (the amount of glue loaded) is: W-dVK. Among them, W represents the theoretical amount of rubber loaded, kg; d represents the density of the mixed rubber, kg/L; V represents the total volume of the mixing chamber, L; K represents the filling factor.
In the production of EPDM reclaimed rubber products, various compounding agents need to be added. Among them, the powdered compounding agent is very loose and the volume and mass are small. The total volume of the compounding agent added in the initial stage of mixing, 2ELYY923, is generally larger than the effective volume of the mixing chamber; the compounding agent The total volume of the rubber decreases with the continuous mixing of the rubber. In actual production, internal mixers strive to make the mixing chamber filling level reach 60%-80% at the end of mixing.
Judging the optimal loading capacity of EPDM reclaimed rubber in the internal mixer can also be judged according to the speed of the top bolt falling and the falling position. Experience has shown that the position of the top bolt to obtain the best amount of glue should be in the first 1/3 of the mixing cycle of each vehicle material. Fluctuate.
From the point of view of process parameters, when EPDM reclaimed rubber or EPDM/EPDM reclaimed rubber is mixed with rubber in an internal mixer, rubber product manufacturers not only need to pay attention to the filling capacity and mixing procedures , Mixing and feeding sequence, mixing temperature, mixing time, energy consumption, rotor speed, top bolt pressure, etc. will all affect the mixing of rubber compounds, and the editor will continue to share related issues with you later.
Exclusive original article [commercial authorization] reprint, excerpt and excerpt in any form are prohibited without written authorization. Focus on Hongyun rubber: learn the process formula and raw material technology of producing rubber products from recycled rubber to help you reduce costs and increase profits