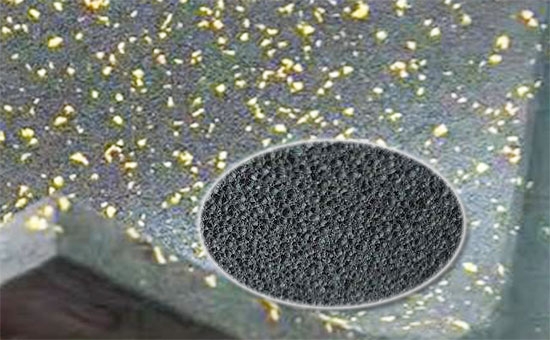
When using latex reclaimed rubber instead of natural rubber to produce foamed foam flooring, a reasonable design formula can increase the amount of latex reclaimed rubber and increase the mechanical strength of the foamed foam flooring. Proper adjustment of the production process can further optimize the quality of the sponge flooring. So in actual production, what compounding agents should be used for foamed foam flooring with latex reclaimed rubber as the main raw material? How much compounding agent is appropriate? How to adjust the mixing process and vulcanization process?
3. Formula design of foam floor containing latex reclaimed rubber
(1) Mixing agent selection: latex reclaimed rubber sponge styrofoam board generally uses sulfur vulcanization. This is because the mechanical strength of peroxide DCP vulcanizates is low, and the low molecular product acetophenone produced after vulcanization is not easy to volatilize and has odor ; Sulfur vulcanized rubber has high mechanical strength, good elasticity and low odor. With high styrene 2LLYY925 to further improve the hardness and tensile stress of the foam foam rubber sheet; clay as a filler can improve the processing performance of the rubber material, and the foam foam rubber sheet has higher viscosity, greater stiffness and lower shrinkage.
Sponge foam flooring using latex reclaimed rubber as the main raw material is mostly foamed with foaming agent H, matched with suitable rubber colorants, and naphthenic oil is selected to soften and plasticize to ensure uniform foaming, bright colors and avoid discoloration. migrate.
(2) Dosage of compounding agent: When using latex reclaimed rubber alone to produce sponge flooring, the amount of sulfur is usually controlled between 1.5-2 parts, and the amount of foaming agent H is controlled between 0.8-1 parts. By adjusting the vulcanizing agent and accelerator The dosage is to coordinate the foaming speed and vulcanization speed of the foamed floor; use 10-25 parts of high styrene to improve the mechanical strength of the floor, and the amount of clay is generally controlled between 30-50 parts; choose 5-10 parts of naphthenic oil to improve Rubber material process performance; use 2-3 parts of rubber coloring agent together.
4. Production process of foam floor containing latex reclaimed rubber
Latex reclaimed rubber has better fluidity and higher plasticity than natural rubber. It is not prone to vulcanization and early vulcanization during vulcanization. The vulcanized rubber has small expansion and contraction and better comprehensive product performance. It should be noted that when latex reclaimed rubber is used with other types of rubber to produce foam styrofoam sheets, rubber product manufacturers need to fully masticate the original rubber before mixing with reclaimed rubber; adjust the production process parameters in time according to climate changes For example, the mixing temperature and vulcanization temperature need to be appropriately increased in autumn and winter compared with summer.
High-quality reclaimed latex rubber, reasonable product formulations and appropriate production processes are important links to ensure the performance and service life of the latex reclaimed sponge foam board. Later editors will have the opportunity to continue to talk with you about the specific application skills of latex reclaimed rubber in sponge foam rubber products.
Exclusive original article [commercial authorization] reprint, excerpt and excerpt in any form are prohibited without written authorization. Focus on Hongyun rubber: learn the process formula and raw material technology of producing rubber products from recycled rubber to help you reduce costs and increase profits