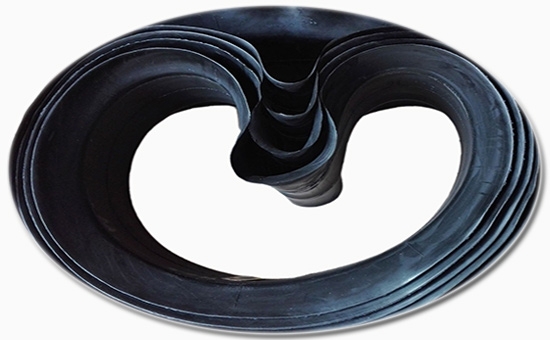
Reclaimed rubber is an ideal raw material for reducing costs in the rubber products industry. In actual production, the reclaimed tire rubber processed from waste tires has good compatibility with natural rubber, styrene butadiene rubber and other general synthetic rubbers. It can be used together with natural rubber and styrene butadiene rubber to prepare tire cushion rubber, which effectively reduces the cost of raw materials. In actual production, appropriately adjusting the formula of the cushion rubber containing tire reclaimed rubber and adjusting the production process can further improve the comprehensive performance of the finished rubber cushion.
1. Formulation adjustment
(1) Add a small amount of butadiene rubber
Butadiene rubber is a synthetic rubber with a regular structure and a cis structure content of more than 95%, which is polymerized by butadiene. Compared with natural rubber and styrene butadiene rubber, vulcanized rubber has better cold resistance, abrasion resistance, and elasticity. Less heat under load. Adding a certain amount of butadiene rubber to the combined tyre reclaimed rubber/natural rubber/styrene butadiene rubber compound can significantly improve the flexural resistance of the compound. In actual production, the recommended ratio of natural rubber, styrene butadiene rubber and butadiene rubber is 3:6:1.
(2) Appropriately increase the amount of reclaimed tire rubber
The purpose of using reclaimed rubber in tire pad rubber is to reduce the cost of raw materials. In actual production, the high-strength reclaimed rubber 2YLYY63 made from tire tread rubber powder of more than 900 has high mechanical strength and good elasticity, which can further improve the tensile strength of the cushion rubber and other indicators. In actual production, 150-230 parts of tread reclaimed rubber can be added to 100 parts of raw rubber (the total amount of natural rubber, styrene butadiene rubber and butadiene rubber). Appropriate increase in the amount of reclaimed rubber will not cause the mechanical strength of the tread rubber. The problem of falling.
(3) Increase the amount of calcium carbonate appropriately
The amount of rubber filler is second only to rubber raw materials in the production of rubber products, and calcium carbonate is the most common filler. In the production of tire cushion rubber, the addition of calcium carbonate can not only reduce the cost of raw materials, but also further improve the heat resistance and dimensional stability of the cushion rubber. When using reclaimed tire rubber/natural rubber/styrene butadiene rubber/butadiene rubber and using rubber to prepare tire cushion rubber, the amount of calcium carbonate is generally controlled at 30-50 parts. To further improve the overall performance of the cushion tape, manufacturers can use activated calcium carbonate or nano-calcium carbonate.
2. Production process
When using reclaimed tire rubber and general-purpose rubber to prepare tire cushion rubber, it is necessary to appropriately adjust the production process, especially the rubber mixing process and the vulcanization process, including controlling the feeding sequence, adjusting the mixing temperature, the vulcanization temperature, and so on. In actual production, generally, natural rubber, styrene butadiene rubber, and reclaimed rubber are first added to the internal mixer for mixing for a specific period of time, then small materials, solid softeners, and half of the carbon black are added to continue mixing, and then the remaining carbon black is added for mixing. Then add softener and mix for a certain period of time before discharging.
Whether there are other ways to improve the comprehensive physical properties of the cushion rubber containing tire reclaimed rubber, I look forward to discussing with you in the later period.
Exclusive original article [commercial authorization] reprint, excerpt and excerpt in any form are prohibited without written authorization. Focus on Hongyun rubber: learn the process formula and raw material technology of producing rubber products from recycled rubber to help you reduce costs and increase profits