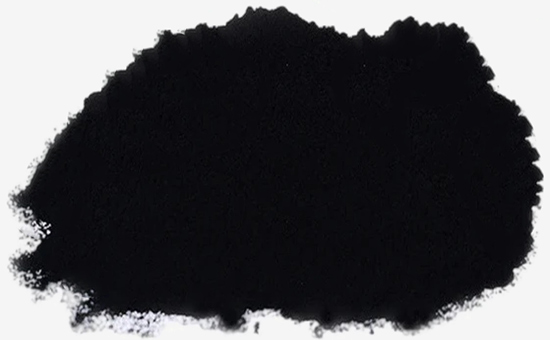
Carbon black is a commonly used reinforcing filler in the production of recycled rubber products, which can not only improve the mechanical properties of reclaimed rubber, such as improving the tensile strength, wear resistance and tear resistance of reclaimed rubber products, but also affect the rubber mixing process and the comprehensive performance of finished products. In actual production, different varieties of carbon black have different surface properties and different effects on the mixing of reclaimed rubber, which is mainly reflected in the mixing process and viscosity of the compound.
1. The influence of carbon black properties on the mixing process of reclaimed rubber
(1) The influence of carbon black particle size on the mixing process of reclaimed rubber: when reclaimed rubber products are reinforced with carbon black, the smaller the particle size of carbon black, the larger the specific surface area, the larger the area that needs to be wetted, and the finer the carbon black unit energy consumption at the same filling volume fraction, the greater the unit energy consumption. Therefore, the finer the particle size, the more difficult it is to mix carbon black, and the more difficult it is to disperse due to slow feeding, high energy consumption, and high heat generation.
(2) The influence of carbon black structure on dispersion: the structural characteristics of carbon black include its morphology, chain connection, etc., which directly affect the fluidity and processability of rubber. The high structure of carbon black void volume is large, it takes more E4LYY1015 time to remove the air in it, once eaten, the high structure of carbon black is easy to disperse. Therefore, when the reclaimed rubber is mixed, the high structure is slower than the low structure, but the dispersion is fast.
(3) The influence of the chemical properties of the carbon black surface on the mixing of reclaimed rubber: the number of functional groups attached to the surface of carbon black and its properties determine the compatibility of carbon black and rubber. Increasing the polar groups on the surface of carbon black can enhance its interaction with rubber and improve the comprehensive properties of reclaimed rubber.
2. The effect of carbon black properties on the viscosity of reclaimed rubber compound
The flow viscosity of the reclaimed rubber compound is very important for the processing process; Generally, the finer the carbon black particles, the higher the structure, the larger the filling amount, the higher the surface activity, and the higher the viscosity of the compound. The finer the carbon black particles, the larger the specific surface area, and the higher the viscosity of the rubber compound.
3. The effect of carbon black dosage on the mixing of reclaimed rubber
Excessive use of carbon black will cause problems such as difficulty in mixing reclaimed rubber, increased energy consumption, and prolonged processing cycle, and will also affect the rheological properties of the rubber compound, resulting in a decrease in the processing performance of the finished product. The amount of carbon black in the production of reclaimed rubber products is generally controlled at 30%-70%, and the amount of carbon black added can be appropriately increased for recycled rubber products with high wear resistance requirements.
When carbon black is used for reclaimed rubber products, the performance and dosage of carbon black not only affect the reclaimed rubber mixing process, but also affect the vulcanization process.
Exclusive original article [commercial authorization] reprint, excerpt and excerpt in any form are prohibited without written authorization. Focus on Hongyun rubber: learn the process formula and raw material technology of producing rubber products from recycled rubber to help you reduce costs and increase profits