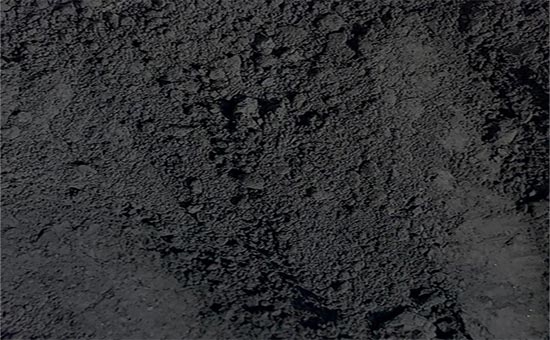
The use of nitrile rubber can be used to produce oil-resistant, wear-resistant, shock-absorbing products, etc., with a wide range of applications. Among them, the compression deformation performance of nitrile vulcanizate directly affects the performance of rubber products, especially sealing products such as rubber oil seals and oil-resistant diaphragms. In actual production, carbon black is used as a commonly used reinforcing agent. Products with different varieties and different dosages have different effects on the compression deformation of nitrile vulcanizates. Rubber products manufacturers should choose suitable carbon black varieties and reasonably determine the amount of carbon black.
1. The effect of carbon black varieties on the compression deformation of nitrile vulcanizates
There are many varieties of carbon black, and the surface properties and particle structure of different types of carbon black vary greatly. When carbon black is used in nitrile rubber products, the overall trend is to reduce the compression set of vulcanized rubber. The order of the effect of various types of carbon black on the compression deformation of nitrile vulcanizate 2YLYY57 is: fine particle thermal black> medium particle thermal black or medium super wear-resistant carbon black> fine particle furnace black, fast pressing black or high resistance Grinding carbon black> semi-reinforcing carbon black.
In actual production, the influence of channel carbon black on the compression deformation of nitrile vulcanizate is basically the same as that of super wear-resistant carbon black. The effect of carbon black on the compression deformation of nitrile rubber compound can be summarized as high structure degree>low structure degree, small particles>large particles.
2. The effect of the amount of carbon black on the compression deformation of nitrile vulcanizates
The amount of carbon black affects the compression set of the nitrile vulcanizate. When nitrile rubber products use reinforcing carbon black such as high abrasion furnace black and channel black, the compression deformation in hot air increases with the increase of the amount of carbon black. The compression set of nitrile vulcanizate in hot oil increases with the increase of carbon black. The amount of black increases and decreases.
Other types of carbon black are used in the production process of nitrile rubber products: when the amount of carbon black in the hot air is less than 75 parts, the compression set of nitrile vulcanizate will decrease with the increase of the amount of carbon black; when the amount of carbon black is 75-100 parts , The compression deformation of nitrile vulcanizate increased significantly. When in hot oil, the compression set of the nitrile vulcanizate will increase with the increase of the amount of carbon black.
Many nitrile rubber products use nitrile reclaimed rubber to reduce the cost of raw materials. The expansion and contraction of unvulcanized rubber mixed with reclaimed rubber during processing is much smaller than that of pure unvulcanized rubber, and the processing is easier. The shape and size of the finished product more precise. Carbon black is an important additive to improve the physical and mechanical properties of nitrile rubber products, especially the combined use of nitrile rubber/reclaimed rubber; when using carbon black to improve the tensile strength and hardness of vulcanized rubber, the change in compression deformation of the rubber must be considered .
Exclusive original article [commercial authorization] reprint, excerpt and excerpt in any form are prohibited without written authorization. Focus on Hongyun rubber: learn the process formula and raw material technology of producing rubber products from recycled rubber to help you reduce costs and increase profits