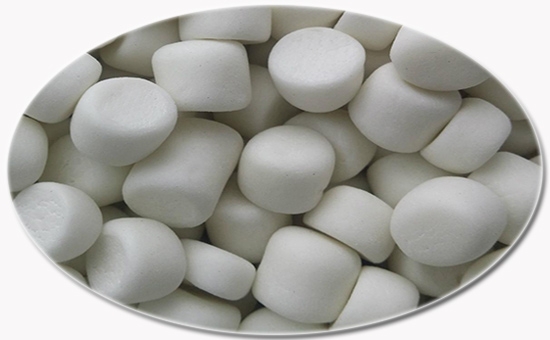
When using reclaimed rubber to produce rubber products, the vulcanization temperature is usually increased by 10 ℃, and the vulcanization time will be shortened by half; therefore, the vulcanization efficiency of reclaimed rubber products with high temperature and rapid vulcanization is higher, and it is favored by manufacturers of reclaimed rubber products. However, in actual production, not all reclaimed rubber products can choose high-temperature rapid vulcanization; even if high-temperature rapid vulcanization can be selected, the variety and amount of compounding agents in the reclaimed rubber product formulation must be carefully selected.
1. Reclaimed rubber products need to be considered when selecting high temperature and rapid vulcanization
When the rubber is vulcanized at a temperature above 160°C, the continuous increase in temperature will cause the crosslink density of the vulcanized rubber to decrease. In actual production, temperature has different effects on the properties of different types of reclaimed rubber, and the vulcanization limit temperature of reclaimed rubber is not the same; the increase of vulcanization temperature will increase the probability of vulcanization. Therefore, not all reclaimed rubber products can choose high-temperature rapid vulcanization. It needs to be determined by combining the processing temperature of reclaimed rubber, the index requirements of reclaimed rubber products and the characteristics of reclaimed rubber vulcanization.
2. Types of reclaimed rubber products suitable for high temperature and rapid vulcanization
High-temperature rapid vulcanization generally refers to vulcanization performed at a temperature of 180-240°C, which has the characteristics of fast vulcanization speed and high vulcanization efficiency. EPDM reclaimed rubber products, butyl reclaimed rubber products and nitrile reclaimed rubber products can try to choose high temperature and rapid 2LLYY1015 vulcanization. In actual production, reclaimed rubber often uses high-temperature rapid vulcanization methods to produce injection products and extruded cables.
3. Common compounding agents for high-temperature rapid vulcanization reclaimed rubber products
Because the traditional sulfur vulcanization system is prone to vulcanization inversion under high temperature conditions, the reclaimed rubber products that choose high temperature and rapid vulcanization generally adopt an effective vulcanization system or a semi-effective vulcanization system, and choose the sulfur carrier DTDM to replace part of the sulfur, and use sulfenamides. Accelerators or thiazole accelerators are the main ones. The use of accelerant TMTD can better adjust the scorch time, crosslinking degree and vulcanization rate, and improve the high-temperature vulcanization effect. Appropriate use of anti-scorching agents such as CTP can better ensure the production safety of reclaimed rubber products.
Anti-aging agents can effectively hinder the destruction of thermal oxygen during the vulcanization process to ensure the flatness of the reclaimed rubber vulcanization. Therefore, when reclaimed rubber products choose high-temperature rapid vulcanization, not only need to choose the vulcanization system compounding agent reasonably, but also pay attention to the choice of antioxidant. In general, adding about 1 part of antioxidant to TMTD/zinc oxide can increase the crosslinking density of the reclaimed rubber vulcanizate and improve the flatness of the rubber vulcanization.
The editor will continue to discuss with you about other issues related to high temperature and rapid vulcanization of reclaimed rubber.
Exclusive original article [commercial authorization] reprint, excerpt and excerpt in any form are prohibited without written authorization. Focus on Hongyun rubber: learn the process formula and raw material technology of producing rubber products from recycled rubber to help you reduce costs and increase profits