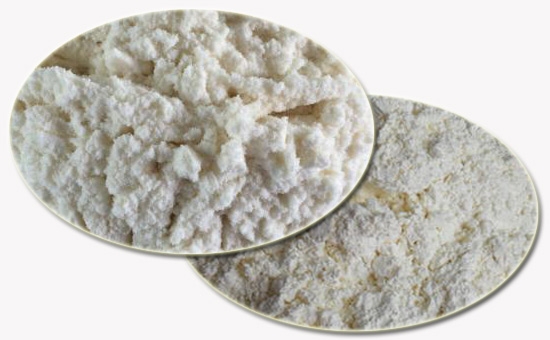
As we all know, scorch inhibitors are functional operating aids to prevent scorching of rubber materials during the production of rubber products, which can effectively control scorch time and prevent scorch. Scorch inhibitors commonly used in the rubber products industry include CTP, oxalic acid, succinic acid, phthalic anhydride, and salicylic acid. Rubber accelerators can accelerate the crosslinking reaction between vulcanizing agents and rubber molecules to achieve the effect of shortening the vulcanization time and lowering the vulcanization temperature. Its use directly affects the safety of rubber processing. Different types of accelerators affect the safety of rubber scorch Different, need to cooperate with different varieties of anti-scorching agent to prevent scorch.
1. Vulcanization system suitable for anti-scorching agent CTP
Scorch inhibitor CTP is widely used in natural rubber, synthetic rubber, and recycled rubber products. It has high activity, can effectively prevent scorching of rubber compounds, and improve production efficiency; to a certain extent, it can restore rubber compounds that have been subjected to high heat or slight scorching. . The sulfenamide accelerator has a long scorch time and high processing safety. A small amount of scorch inhibitor CTP can be used to obtain a good scorch prevention effect in a vulcanization system containing such accelerators such as NOBS.
In actual production, the anti-scorching agent CTP has a high activity and a small amount, which basically does not affect the vulcanization efficiency of rubber products and the physical properties of finished products.
2. Vulcanization system suitable for scorch inhibitor HTM
The anti-scorching agent HTM and CTP have the same anti-scorching mechanism in rubber, and the activity is higher than CTP. It is widely used in various types of rubber. It contains thiocarbamate accelerators, dithiophosphate accelerators, and Sulfonamide accelerators and thiazole accelerators and other high-efficiency accelerators 2LLYY623 have good anti-scorching effect, which can effectively increase the rubber Mooney scorch time, delay the vulcanization start time at the vulcanization temperature, and will not affect the use process Curing process and physical and mechanical properties of vulcanized rubber.
3. Vulcanization system suitable for scorch inhibitor NA
The anti-scorch agent NA, namely N-nitrosodiphenylamine, is a variety of anti-scorch agents commonly used in the production of rubber products. It can show good anti-scorch effect in vulcanization systems containing sulfenamide accelerators. The anti-scorching agent needs to pay attention to the vulcanization temperature during use: due to the reduced activity of the anti-scorching agent NA under conditions of more than 100℃, the anti-scorching effect is not great in the environment of 120℃, under the processing conditions of 135℃ Decomposition loses its activity. The gas released after decomposition will also cause porosity in rubber products. Therefore, the high-temperature vulcanization system cannot use the scorch inhibitor NA.
4. Suitable curing system for salicylic acid and phthalic anhydride
When salicylic acid and phthalic anhydride are used as anti-scorching agents in the production of rubber products, they have a certain anti-scorching effect on vulcanization systems containing guanidine accelerators and thiazole accelerators. Among them, the anti-scorching effect of phthalic anhydride is higher than that of salicylic acid. The effect is good. It should be noted that the dispersion of phthalic anhydride in the rubber compound is poor, and there are side effects of delayed vulcanization and reduced physical properties of vulcanized rubber during use; phthalic anhydride containing sulfenamide accelerators and thiazole accelerators The anti-coking effect in the vulcanization system is very small, so it is not recommended.
When using natural rubber, synthetic rubber or recycled rubber to produce various types of rubber products, the vulcanization system containing high-efficiency rubber accelerators must add an appropriate amount of anti-scorching agent to prevent scorching of the rubber compound and improve the production safety and efficiency of rubber products. Yield.
Exclusive original article [commercial authorization] reprint, excerpt and excerpt in any form are prohibited without written authorization. Focus on Hongyun rubber: learn the process formula and raw material technology of producing rubber products from recycled rubber to help you reduce costs and increase profits