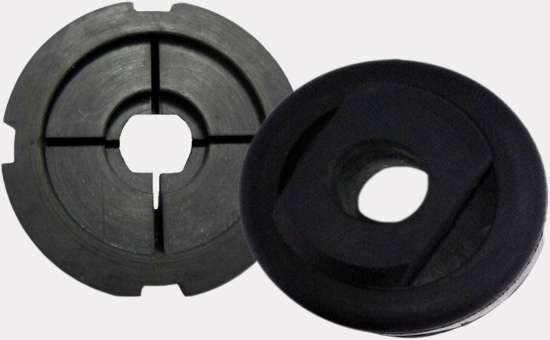
Isoprene reclaimed rubber has the dual characteristics of natural rubber and synthetic rubber, and its price is much lower than that of original rubber. It is widely used in tire manufacturing, medical rubber products, rubber sheets, tapes, hoses, adhesives, craft rubber products, etc. Significantly reduce raw material costs. When using PP reclaimed rubber to produce cost-effective rubber products, it is of great significance to further improve the quality and quality of the isoprene recycled rubber products by reasonably selecting the type and amount of accelerators in the vulcanization system.
1. A vulcanization accelerator commonly used for isoprene reclaimed rubber
When using isoprene reclaimed rubber to produce rubber products, sulfenamide accelerators have long scorch time and high processing safety, and the mechanical properties and aging resistance of reclaimed vulcanizates after vulcanization are better; sulfenamide accelerators As the main accelerator, the thiuram 1JLYY1115 accelerator is used in combination to increase the vulcanization rate. In actual production, the thiazole accelerator-thiuram accelerator is used in combination, the vulcanizate has poor physical and mechanical properties, and the vulcanization rate is difficult to reach the expected standard; the isoprene reclaimed rubber product often uses an amine accelerator. Two or more vulcanization accelerators are used together with a better vulcanization effect.
2. Isoprene reclaimed rubber and natural rubber combined with accelerator
There are many differences between PP reclaimed rubber and natural rubber. In addition to a large number of effective rubber hydrocarbons, natural rubber also includes fatty acids and proteins, which can be activated during the vulcanization process. However, in the isoprene reclaimed rubber, there is no vulcanization. HY fatty acids, proteins and other substances that act as activating agent, so the vulcanization rate is generally slower than that of natural rubber, and an appropriate amount of vulcanization accelerator is required. When the isoprene reclaimed rubber is used together with the natural rubber, the amount of sulfur should be appropriately reduced, and the amount of sulfur should be controlled below 2.5 parts to avoid the problem of mechanical strength drop caused by excessive sulfur usage; when the reclaimed rubber/natural rubber is selected for sulfur vulcanization, the accelerator is used. CZ, NOBS, TMTM, TMTD, TETD, MZ, PZ, M, DM, etc. cooperate better.
In the production process of isoprene reclaimed rubber products, not only one, two or more vulcanization accelerators are required, but the zinc oxide/stearic acid co-use system also often appears as a vulcanization aid, and the amount of zinc oxide is usually about 5 parts. Use 2-3 parts of stearic acid.
In the production process of isoprene recycled rubber products, the type and amount of vulcanization accelerator directly affect the quality of vulcanized rubber vulcanizate, vulcanization efficiency, etc. Rubber products manufacturers must choose a suitable vulcanization accelerator to adjust the vulcanization speed of PP reclaimed rubber vulcanizate. To further optimize the quality of recycled rubber products.
Exclusive original article [commercial authorization] reprint, excerpt and excerpt in any form are prohibited without written authorization. Focus on Hongyun rubber: learn the process formula and raw material technology of producing rubber products from recycled rubber to help you reduce costs and increase profits