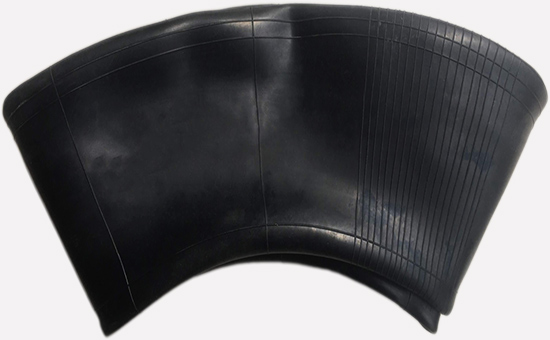
Butyl rubber has good air tightness and heat resistance, and is an ideal raw material for the production of rubber inner tubes; however, butyl rubber has low mechanical strength and slightly poor ozone resistance. The degree of softening due to thermal oxidative aging during running under load is reduced. Butyl reclaimed rubber is processed with butyl inner tube as the main raw material. It is resistant to air permeability, heat resistance and aging. It can be mixed into butyl rubber/EPDM inner tube to effectively reduce product quality under the premise of ensuring product quality. Raw material costs.
1. Mix 10 parts of butyl reclaimed rubber to produce IIR/EPDM inner tube formula
90 parts of butyl rubber, 10 parts of EPDM rubber, 10 parts of butyl reclaimed rubber, 5 parts of zinc oxide, 1.5 parts of stearic acid, 50 parts of carbon black N660, 15 parts of paraffin oil, 4 parts of petroleum resin, accelerator 0.5 part of M, 1.5 part of promoting TDTD, 1.5 part of sulfur; total: 189 parts. Vulcanization time: 150℃×30min.
2. Using 25 parts of butyl reclaimed rubber to produce IIR/EPDM inner tube formula
90 parts of butyl rubber, 10 parts of EPDM rubber, 25 parts of butyl reclaimed rubber, 5 parts of zinc oxide, 1.5 parts of stearic acid, 35 parts of carbon black N 550, 35 parts of carbon black N 774, 25 parts of paraffin oil , 2 parts of petroleum resin, 0.5 part of accelerator DM, 1.5 part of accelerator TMTD, 1.5 part of sulfur; total: 232 parts. Vulcanization time: 150℃×30min.
3. Blending 45 parts of butyl reclaimed rubber to produce IIR/EPDM inner tube formula
90 parts of butyl rubber, 10 parts of EPDM rubber, 45 parts of butyl reclaimed rubber, 4 parts of zinc oxide, 1.2 parts of stearic acid, 1.3 parts of active agent, 1 part of antioxidant, 32 parts of carbon black N 550, carbon black 33 parts of black N774, 13 parts of naphthenic oil, 0.5 part of accelerator M, 1 part of accelerator TMTD, 2 parts of sulfur; total: 234 parts. Vulcanization time: 160℃×10min.
4. The function and skills of IIR/EPDM inner tube mixed with butyl reclaimed rubber
The main purpose of using butyl reclaimed rubber in the production of IIR/EPDM inner tubes is to reduce costs. Compared with IIR/EPDM combination rubber, the compound rubber mixed with butyl reclaimed rubber has less shrinkage and deformation after extrusion and better dimensional stability; therefore, butyl reclaimed rubber 2ELYY324 can also improve the processing technology of rubber inner tube to a certain extent. In actual production, because the filtration of butyl reclaimed rubber is difficult, it is necessary to select a suitable particle size for filtration of butyl reclaimed rubber, reasonably control the amount of butyl reclaimed rubber, and reduce costs on the premise of ensuring quality.
Incorporating butyl reclaimed rubber into IIR/EPDM inner tubes to replace part of butyl rubber can not only reduce the amount of high-priced butyl rubber, but also improve the process performance of the compound. Later, the editor will continue to share with you the use of butyl reclaimed rubber IIR/EPDM inner tube production process and points to note.
Exclusive original article [commercial authorization] reprint, excerpt and excerpt in any form are prohibited without written authorization. Focus on Hongyun rubber: learn the process formula and raw material technology of producing rubber products from recycled rubber to help you reduce costs and increase profits