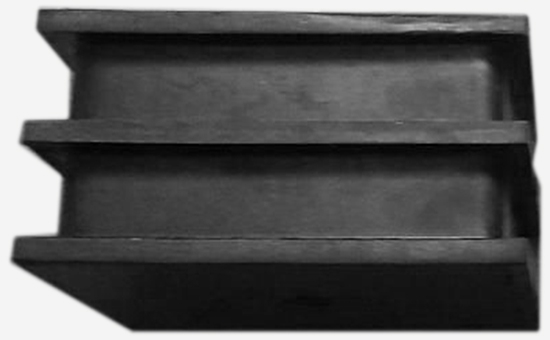
Generally, butyl rubber or chlorinated butyl rubber is used in rubber shock absorbers that require large damping. In actual production, chlorinated butyl rubber has a faster vulcanization speed, better heat resistance, and smaller compression deformation than butyl rubber. It is often used to produce engine base shock absorbers. Reasonable blending of chlorinated butyl rubber shock absorber with chlorinated butyl reclaimed rubber can significantly reduce the cost of raw materials without affecting the physical properties of the engine shock absorber.
1. Reference formula for production of engine shock absorbers with pure chlorobutyl rubber
100 parts of chlorinated butyl rubber, 5 parts of zinc oxide, 0.5 parts of magnesium oxide, 45 parts of high wear-resistant carbon black, 15 parts of MT, 15 parts of paraffin oil, 1 part of accelerator TMTD, 1 part of accelerator DM, 2 parts of sulfur ; Total: 184.5 copies.
2. Basic performance requirements of engine shock absorbers
Rubber engine shock absorbers require the rubber to have high dynamic damping performance and bonding strength, suitable elastic modulus, good fatigue resistance, etc., to ensure good shock absorption and minimize chlorobutyl vulcanization The creep of the rubber prolongs the service life of the shock absorber. When using chlorinated butyl reclaimed rubber to replace part of chlorinated butyl rubber, rubber product manufacturers need to start from the actual needs of engine shock absorbers and select chlorinated butyl reclaimed rubber products with appropriate indicators to increase the amount of reclaimed rubber and ensure the finished product quality.
3. Chlorinated butyl rubber/reclaimed rubber engine shock absorber compounding agent selection
(1) Vulcanization system: Chlorinated butyl rubber and chlorinated butyl reclaimed rubber can be co-vulcanized. The vulcanization system of chlorinated butyl shock absorber can choose traditional sulfur vulcanization system. The vulcanized rubber has mechanical strength, abrasion resistance and resistance. Dynamic fatigue performance is better.
(2) Reinforcement system: The damping and rigidity of the chlorinated butyl vulcanizate using high wear-resistant carbon black is better than that of semi-reinforced carbon black. The smaller the particle size of carbon black, the increase in activity and dosage, and the shock absorber The higher the damping performance of 2LLYY1221 and the modulus; it should be noted that the smaller the carbon black particle size, the relatively poor fatigue resistance of the chlorobutyl vulcanizate. In actual production, the engine shock absorber with chlorinated butyl rubber and chlorinated butyl reclaimed rubber as the main raw materials can also use fast-pressed carbon black in an appropriate amount.
(3) Softening system: The use of plasticizers can improve the low-temperature properties and fatigue resistance of the rubber. Too much use will cause the elastic modulus of the chlorobutyl rubber/reclaimed rubber to decrease, and the creep and stress relaxation speed will increase. The damping performance of the shock absorber is affected. Paraffin oil is usually used in chlorinated butyl shock absorbers, and the amount is controlled at 10-15 parts.
3. Processing technology of chlorobutyl rubber/reclaimed rubber engine shock absorber
The mixing and vulcanization process of chlorobutyl rubber/reclaimed rubber affects the quality of the finished product. During mixing, the chlorinated butyl rubber should be fully masticated and then mixed with the chlorinated butyl reclaimed rubber. During mixing, the mixing time should be strictly controlled and the number of rolls should be appropriately reduced. Strictly control the vulcanization temperature and time during vulcanization.
When using chlorinated butyl reclaimed rubber in chlorinated butyl rubber to reduce the production cost of engine shock absorbers, rubber products manufacturers must reasonably control the amount of reclaimed rubber, and cannot reduce the cost at the expense of the quality of the shock absorber. Reasonable use of chlorinated butyl reclaimed rubber can not only reduce the raw material cost of the shock absorber, but also improve the performance of the rubber material and reduce power consumption. It can also improve the performance and life of the engine shock absorber to a certain extent.
Exclusive original article [commercial authorization] reprint, excerpt and excerpt in any form are prohibited without written authorization. Focus on Hongyun rubber: learn the process formula and raw material technology of producing rubber products from recycled rubber to help you reduce costs and increase profits