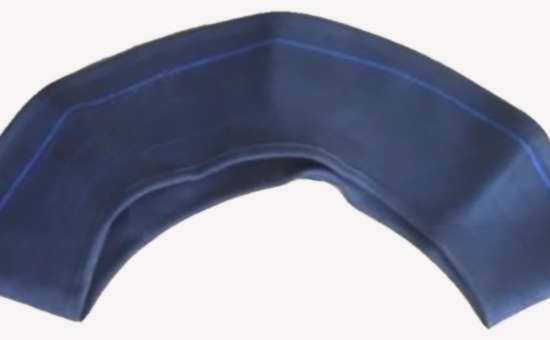
Appropriate use of butyl reclaimed rubber in NR/SBR rubber inner tubes can achieve the dual purpose of improving inner tube performance and reducing costs; adjusting the inner tube formula and production process containing butyl reclaimed rubber can further optimize product quality and reduce more raw material costs. So how should rubber products manufacturers design NR/SBR rubber inner tubes containing butyl reclaimed rubber? How to control various production process parameters?
1. Reference formula of NR/SBR inner tube containing butyl reclaimed rubber
70 parts of natural rubber, 30 parts of styrene-butadiene rubber, 30 parts of butyl reclaimed rubber, 2 parts of stearic acid, 1.5 parts of paraffin, 2.5 parts of antioxidant, 5 parts of tackifier, 40 parts of carbon black, 7 parts of softener, sulfur 1.5 parts, 1.5 parts accelerator; Total: 191 parts.
2. NR/SBR inner tube mixing process with butyl reclaimed rubber
When natural rubber/styrene-butadiene rubber/butyl reclaimed rubber is used together to produce rubber inner tubes, usually the natural rubber is fully masticated and then added to the styrene-butadiene rubber for mixing, and the two are mixed 2LLYY928 evenly and then butyl reclaimed rubber is added for mixing; After uniformly mixing again, the roller pitch of the rubber mixer is controlled to 1-1.5mm for thinning until there are no reclaimed rubber particles, and the triangle bag enters the mixing process. In actual production, the blended rubber material can enter the mixing process only after its plastic value reaches 0.35-0.4.
When the natural rubber/styrene-butadiene rubber/butyl reclaimed rubber is mixed after full plasticization, the discharging temperature is generally controlled of 120-130℃, the mixing time is about 8 minutes, and the next step is to cool for more than 4 hours after the sheet Operation to ensure rubber processing performance and inner tube performance.
3. Extrusion vulcanization of NR/SBR inner tube containing butyl reclaimed rubber
When butyl reclaimed rubber is used in the natural rubber/styrene-butadiene rubber inner tube formula, the vulcanization temperature should be controlled at about 160℃, the vulcanization time should be controlled at about 8min, and the internal pressure should be discharged within 2min. After adding sulfur, the filtered rubber material needs to be parked for more than 4 hours before it can be normally extruded according to the size of the semi-finished product. When extruding, ensure that the extruder barrel is clean and the surface of the extruded semi-finished product is smooth and bright, without particles, and without scorching.
From the performance point of view, mixing an appropriate amount of butyl reclaimed rubber in the NR/SBR inner tube will significantly improve the airtightness and tearability of the finished inner tube, and the product will not leak air or cause adhesion problems after long-term use; from a cost perspective Considering that the price of butyl reclaimed rubber is much lower than that of butyl rubber, natural rubber, and styrene-butadiene rubber; compared with NR/SBR mixed with butyl raw rubber, butyl reclaimed rubber has a better blending effect and lower cost. Later editors will have the opportunity to continue to share with you the application skills of butyl reclaimed rubber in natural rubber/styrene butadiene rubber inner tubes.
Exclusive original article [commercial authorization] reprint, excerpt and excerpt in any form are prohibited without written authorization. Focus on Hongyun rubber: learn the process formula and raw material technology of producing rubber products from recycled rubber to help you reduce costs and increase profits