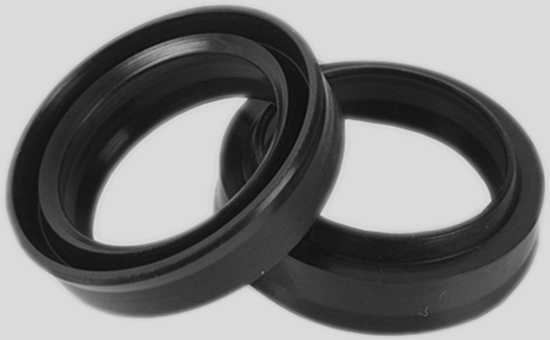
Carbon black is the most commonly used reinforcing filler in rubber products. Different kinds of carbon black have different molecular structure characteristics and different functions in rubber products. Therefore, when using NBR or NBR to produce oil-resistant seals, the types of carbon black have a direct impact on the sealing performance of NBR seals. How does the carbon black affect the sealing performance of nitrile seals? How to choose carbon black when producing nitrile nitrile seals?
The main factors affecting the sealing performance of rubber seals are the elasticity, hardness and compression permanent deformation of rubber materials. Nitrile-butadiene seals mostly work in oil medium for a long time. Therefore, oil resistance is also one of the factors affecting the sealing performance of nitrile-butadiene seals. The effect of oil resistance is of great significance for prolonging the service life of NBR seals.
1. effect of carbon black on elasticity of NBR vulcanizates
Carbon black commonly used in rubber products industry includes trough carbon black, medium-super wear-resistant furnace black, pyrolysis carbon black, etc. Different types of carbon black have different particle sizes and different elasticities. Among them, trough carbon black and furnace black have small relative particle sizes and low elasticity, and pyrolysis carbon black has large particle size, low structure and good elasticity. The best elasticity and resilience are obtained when black is used, and the relatively poor carbon black is obtained when using medium-super abrasion-resistant furnace black with high structural degree. The elasticity of nitrile-butadiene seals is in the order of no carbon black, medium-particle pyrolysis carbon black, fine-particle pyrolysis carbon black, quick-pressing furnace black, fine-particle furnace black, high abrasion-resistant furnace black and medium-super abrasion-resistant furnace black.
2. effect of carbon black type on compression permanent deformation of NBR vulcanizates
Compression permanent deformation is one of the most important indicators for measuring the quality of rubber products, especially rubber sealing products. Rubber seals use compression section deformation to produce stress, and closely combined with the contact surface to play a sealing role. Seals have been in a sealed state in the use process, rubber compression permanent deformation performance directly affects the durability of rubber seals.
The types, properties and dosage of carbon black will affect the compression permanent deformation of nitrile vulcanizates. In practical production, the compression permanent deformation of NBR vulcanizates decreases with the increase of carbon black content. The effects of different types of carbon black on the compression permanent deformation of NBR vulcanizates are as follows: without carbon black or fine particle pyrolysis carbon black, medium particle pyrolysis carbon black, trough carbon black or medium super-abrasion furnace black, fine particle pyrolysis carbon black. Particle furnace black, fast pressure furnace black or high wear resistant carbon black, half reinforcing furnace black. Therefore, in view of the compression and permanent deformation of the rubber, the carbon black should be used for the nitrile seals.
3. effect of carbon black type on the oil resistance of NBR vulcanizate
The smaller the carbon black particles and the higher the activity, the better the oil resistance of the nitrile-butadiene vulcanizates, and the higher the structure of the carbon black, the better the dimensional stability of the nitrile-butadiene vulcanizates.
Different kinds of carbon black have different effects on the elasticity, compression permanent deformation and oil resistance of nitrile-butadiene vulcanizate, and the performance of the same kind of carbon black used in seals working in hot air and in hot oil is also different, so the rubber manufacturer should choose carbon black according to nitrile-butadiene seal when choosing carbon black for nitrile-butadiene seal. Use environment and scope of parts to determine: requirements of good elasticity, compression of small permanent deformation of nitrile-butadiene seals choose semi-reinforced carbon black or pyrolysis carbon black, high tensile strength and wear resistance of the seals using fine particle carbon black, high elongation at break, tear resistance, wear resistance requirements of nitrile-butadiene seals selection The best way to improve the sealing performance of nitrile-butadiene seals is to use different kinds of carbon black together.
Nowadays, more and more manufacturers of nitrile-butadiene sealants begin to add regenerated adhesives in their products, or use high-quality nitrile-butadiene regenerated adhesives to produce sealants. In this section, two points are emphasized: (1) Selecting the regenerated adhesives with stable quality and the closest performance to the seals; (2) Calculating the carbon black content of the regenerated adhesives themselves into The amount of carbon black in the formulation of nitrile seals.
Exclusive original article [commercial authorization] reprint, excerpt and excerpt in any form are prohibited without written authorization. Focus on Hongyun rubber: learn the process formula and raw material technology of producing rubber products from recycled rubber to help you reduce costs and increase profits