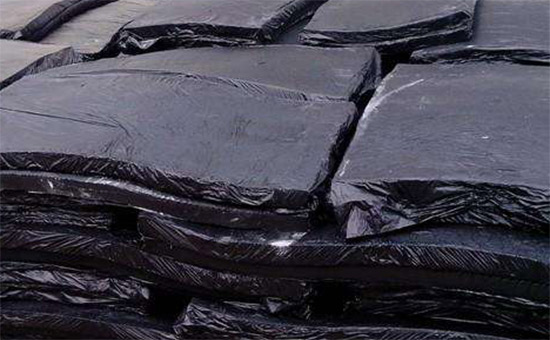
The rubber sole has excellent softness and elasticity. It has obvious shock absorption effect and high comfort during wearing. It is suitable for all kinds of shoe materials. In actual production, rubber soles require good elasticity, abrasion resistance, flexibility, etc., and are mostly processed from natural rubber and synthetic rubber; Recycled rubber, as a substitute for high priced raw rubber, can be mixed into the rubber sole formula in a proper proportion, among which, non migration tire recycled rubber and light color recycled rubber are the most widely used in the sole rubber.
1. Application of non migration tire recycled rubber in black rubber sole
The rubber sole is mostly made of natural rubber/cis polybutadiene rubber or natural rubber/styrene butadiene rubber/cis polybutadiene rubber, and the rubber content is controlled among 35% and 40%. The natural rubber in the black sole is mostly 4 # and 5 #. The recycled tire rubber 1JLYY729 has good compatibility with natural rubber, polybutadiene rubber and styrene butadiene rubber, and can be used together to produce black rubber soles. The problem of discoloration migration will not occur if the recycled tire rubber does not migrate, which is more suitable for the production of rubber soles without discoloration.
Low sulfur and high accelerator system is often used when the non migration tire recycled rubber is used with natural rubber, cis polybutadiene rubber or styrene butadiene rubber to produce black rubber soles. Promoters that can give the rubber good physical and mechanical properties, good vulcanization flatness, anti scorching, pollution-free, non discoloration, and non spraying are used together. Common accelerators are M+D+DM, M+D+CZ. The black rubber sole filler system can use high wear-resistant carbon black in combination with clay, calcium carbonate, soft carbon black, etc. Improve the processability of recycled tire rubber and natural rubber, cis polybutadiene rubber and styrene butadiene rubber. Gumarone resin, second line oil, industrial grease, engine oil, petroleum jelly, pine tar, spindle oil, etc. can be used. Using antioxidant A or antioxidant D can prolong the aging time of black sole containing non migration tire recycled rubber.
2. Application of light color recycled rubber in light color rubber sole
In actual production, light rubber soles are mostly processed with natural rubber as the main raw material, and 1 #, 2 #, 3 # cigarette flake glue or standard glue 1 # or white crepe flake glue are commonly used; Appropriate use of light color recycled rubber is easy to match colors and does not migrate, which can effectively reduce the cost of raw materials and improve the processing performance of rubber compound on the premise of ensuring the use performance of light color sole.
When light color recycled rubber is used to reduce the production cost of light color rubber soles, pollution-free reinforcing agents such as white carbon black, white Yanhua, clay, lignin, etc. are often used; It is recommended to use a small amount of diethylene glycol, glycerin, polyethylene glycol, triethanolamine, etc. when adding white water table. Due to the delayed vulcanization effect of white carbon black and clay, the amount of sulfur used in the light color outsole vulcanization system with sulfur accelerator is slightly more than that in the black rubber outsole. In order to avoid yellowing of the light colored outsole, it is recommended to use non polluting softeners, such as naphthenic oil, paraffin oil, transformer oil, Vaseline, calcium ester, etc; Avoid the use of coal tar, pine tar and other rubber oils that have severe discoloration on the light colored outsole. Select non polluting antioxidant MB, SP, DOD, 246, 2246, etc.
In actual production, when the cost of sole raw materials is reduced by mixing non migration tire recycled rubber and light color recycled rubber, the rubber curing system needs to be properly adjusted according to the rubber hydrocarbon content in the recycled rubber. Generally, 1.0-1.5 parts of sulfur, 2-3 parts of zinc oxide and 0.5-0.9 parts of quasi accelerator are added for every 100 parts of recycled rubber. The following Xiaobian will continue to share with you the differences among the formula design and production process of producing rubber soles with non migrating recycled tire rubber and light colored recycled rubber.
Exclusive original article [commercial authorization] reprint, excerpt and excerpt in any form are prohibited without written authorization. Focus on Hongyun rubber: learn the process formula and raw material technology of producing rubber products from recycled rubber to help you reduce costs and increase profits