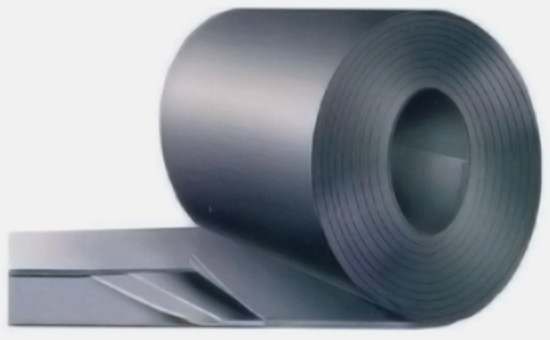
Conveyor belt is one of the rubber products used in a large amount of raw materials, the use of natural rubber production conveyor belt is not only high prices, but also very unstable raw material costs, bring some trouble to the conveyor belt manufacturers. The use of recycled rubber instead of natural rubber to produce conveyor belts can reduce raw material costs while ensuring product quality. However, some manufacturers react with the use of reclaimed rubber belts wear resistance performance standards, is the quality of reclaimed rubber products? This is not the case. The wear resistance of the conveyor belt is affected by many factors.
There are three main forms of wear on conveyor belts: wear wear, fatigue wear, and take-up wear. These three types of wear are all related to the main mechanical properties of rubber materials. Therefore, when choosing a reclaimed rubber product, formula design must be achieved. The overall balance between performance.
First of all, we must choose the right index of reclaimed rubber products. The conveyor belt is mainly used in cement, coking, metallurgy, chemical industry, iron and steel industries where the conveying distance is short and the conveying volume is small. Therefore, the reclaimed rubber strength index of the production conveyor belt should be up to the standard. The high-strength reclaimed rubber product can give the conveyor belt good impact resistance, especially wear resistance, and can extend its service life.
Secondly, in order to select the appropriate vulcanization system, the wear resistance of the rubber compound has an optimal value as the crosslinking density increases. The optimum value depends not only on the vulcanization system but also on the amount and structure of carbon black. The concept of the optimal stiffness of the wearability explains that when the amount and structure of carbon black are increased, the stiffness provided by the carbon black increases, and if the optimum value of the stiffness of the vulcanizate is maintained, the vulcanization system must be reduced. The rigid part provided is to properly reduce the cross-linking density, whereas the cross-linking density of the rubber should be increased on the contrary, and the test shows that the more mono-sulfur bonds are contained, the better the abrasion resistance of the rubber is, and the conveyor belt produced is also more resistant. mill.
Finally, the filling system is adjusted. Generally, the wear resistance of the rubber material decreases with the particle size of the carbon black and increases with the increase of the surface activity and dispersibility. The carbon black vulcanizate is added to the rubber material of the nylon conveyor belt and the wear resistance thereof is improved. The wear resistance of carbon black is twice as high as that of filling carbon black. The influence of the structure of carbon black on the wear resistance of the rubber compound is not uniform and remains to be further studied. There is also an optimum value for the amount of carbon black used and the wear resistance of the rubber compound. The optimum amount of carbon black, which is generally used as a high-friction belt covering rubber, increases with the severity of use conditions, and is filled with a new process carbon black and used. Silica coupling agent-treated silica can improve the wear resistance of strength heat-resistant conveyor belts.
Exclusive original article [commercial authorization] reprint, excerpt and excerpt in any form are prohibited without written authorization. Focus on Hongyun rubber: learn the process formula and raw material technology of producing rubber products from recycled rubber to help you reduce costs and increase profits