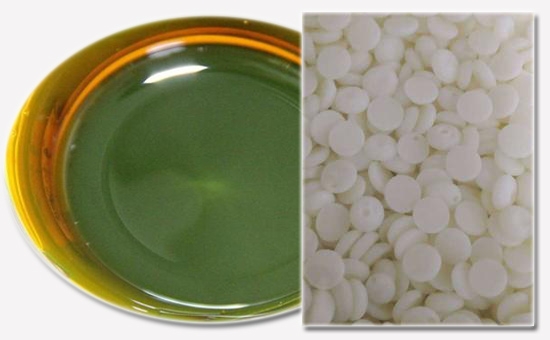
The use of reclaimed rubber to produce rubber products requires the cooperation of a variety of rubber additives, among which processing modifiers can improve the processing performance of reclaimed rubber, ensure the smooth progress of the processing and molding process of reclaimed rubber products, reduce production energy consumption, shorten production time, and Productivity. Commonly used processing modifiers in the production of reclaimed rubber products include lubricants, release agents, dispersants, softeners, peptizers, etc. Different additives have different functions in the production of reclaimed rubber products.
1. Lubricant
In the production process of reclaimed rubber products, lubricants can reduce the friction between processing equipment and reclaimed rubber and improve the fluidity of reclaimed rubber to facilitate molding and demolding. Common lubricants include paraffin wax, polyethylene wax, oxidized polyethylene wax 2LLYY1118 and other hydrocarbon lubricants, as well as fatty acids, fatty alcohols, fatty amides, fatty acid esters, fatty acid soaps, etc.
2. Release agent
As the name suggests, the role of the release agent in the production of reclaimed rubber products is to help the products to be demolded smoothly and to improve the surface finish of the reclaimed rubber products. The release agent can be directly coated on the surface of the mold or molding machine (coated release agent), or added to the polymer (internal release agent); silicone oil substances are commonly used release agents in the product industry.
3. Dispersant
In the production process of reclaimed rubber products, the degree of dispersion of vulcanizing agents, accelerators, fillers, colorants and other rubber compounding agents in the rubber compound directly affects the performance of the finished reclaimed rubber products. Adding an appropriate amount of dispersant can promote the uniform dispersion of compounding agents, especially in In reclaimed rubber products with large amounts of fillers, color masterbatches and colorants. Common dispersants include hydrocarbon dispersants such as paraffin oil, polyethylene wax, and oxidized polyethylene wax, as well as fatty acid soaps, fatty acid esters, and fatty amides.
4. Softener
The role of softeners in the production of reclaimed rubber products is to improve rubber processing performance. Common products include petroleum-based softeners such as naphthenic oil and aromatic oil, coal tar-based softeners such as coumarone, coal tar, etc., and fatty oils Department softeners such as vegetable oils, fatty acids, etc.
5. Peptizer
Some reclaimed rubber products need to use peptizers in the production process. Such processing modifiers are used in a small amount, which can significantly improve the plasticity of the rubber and shorten the plasticizing time. In actual production, thiophenol compounds, alkylphenol disulfides and aromatic disulfides are common peptizers.
Processing modifiers can significantly improve the processing performance of reclaimed rubber, reduce energy consumption, and increase efficiency. They are indispensable additives in the production process of reclaimed rubber products. Later editors have the opportunity to continue to share with you the commonly used processing and modification Specific application skills of additives.
Exclusive original article [commercial authorization] reprint, excerpt and excerpt in any form are prohibited without written authorization. Focus on Hongyun rubber: learn the process formula and raw material technology of producing rubber products from recycled rubber to help you reduce costs and increase profits