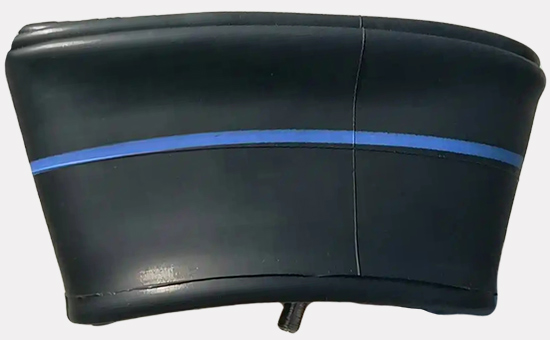
When using butyl recycled rubber as the main raw material to produce rubber products, the sulfur vulcanization system is one of the commonly used vulcanization systems, with good processing performance and good physical and mechanical properties of vulcanized rubber. When choosing sulfur vulcanization system for butyl reclaimed rubber, the commonly used accelerators are DM, DPG, TMTD, etc., and it is necessary to select the appropriate accelerator according to the specific product requirements and processing conditions, and zinc oxide is commonly used as the activator; Appropriate adjustment of the dosage of sulfur, accelerator and activator can further optimize the comprehensive performance of butyl recycled rubber products.
When sulfur vulcanization is used in butyl reclaimed rubber products, the amount of sulfur is generally controlled at about 2-3 parts, and vulcanized rubber can obtain good mechanical strength and ozone resistance. It should be noted that the solubility of sulfur E4LYY228 in butyl rubber is low, and the total amount of sulfur is more than 1.5 parts, which can easily cause frosting. Therefore, butyl reclaimed rubber and butyl rubber are used together, especially when the proportion of butyl rubber is large, the amount of sulfur is generally controlled at about 1.5-2 parts.
1. Butyl reclaimed rubber is commonly used in ordinary sulfur vulcanization system
The butyl reclaimed rubber vulcanized by sulfur vulcanization system mostly produces polysulfide bonds and disulfide bonds, and the physical and mechanical properties of vulcanized rubber are good, but the heat resistance of vulcanized rubber is poor. Commonly used combinations: 0.5-2 parts of sulfur, 0.5-1.5 parts of dithiocarbamate or thiuram accelerators, 0.5-1.5 parts of thiazole accelerators.
2. Butyl reclaimed rubber sulfur donor vulcanization system
The use of sulfur donor vulcanization of butyl reclaimed rubber can endow the vulcanized rubber with excellent heat resistance and small compression set. Insufficient crosslinking during vulcanization, lower tensile strength and higher cost. Commonly used combinations: 2 parts of dithiomorphine and thiuram tetrasulfide, 2 parts of thiuram and dithiocarbamate.
3. Butyl reclaimed rubber low sulfur and high vulcanization system
The physical properties of the butyl reclaimed rubber vulcanized by the low-sulfur and high-pro-vulcanization system were among the ordinary sulfur vulcanization system and the sulfur donor vulcanization system. Commonly used formulation: 0.3-0.5 parts sulfur, 0.2-1 parts thiazole accelerator, 3-4 parts thiuram or dithiocarbamate accelerator.
The dosage of zinc oxide is generally about 5 parts. It is necessary to use an appropriate amount of stearic acid, but the dosage of stearic acid is not recommended to exceed 3 parts, because too much will affect the constant tensile stress of vulcanized rubber.
After determining the type and amount of vulcanizing agent, one or several main accelerators can be used in combination with an auxiliary accelerator to better coordinate the relationship among vulcanization speed, crosslinking density, scorch safety and vulcanized rubber performance. In the future, we will continue to share with you the varieties and application points of commonly used accelerators for butyl reclaimed rubber products.
Exclusive original article [commercial authorization] reprint, excerpt and excerpt in any form are prohibited without written authorization. Focus on Hongyun rubber: learn the process formula and raw material technology of producing rubber products from recycled rubber to help you reduce costs and increase profits