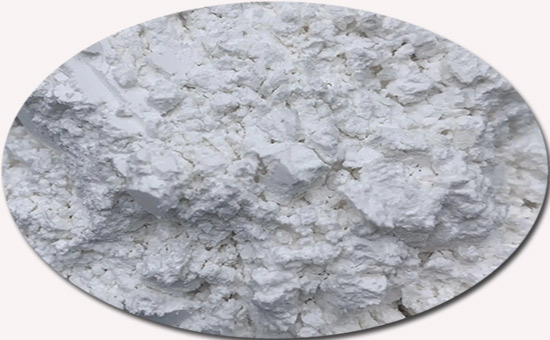
The regenerated nitrile rubber has excellent oil resistance and can be used alone or in combination with nitrile rubber to produce oil resistant rubber products, effectively reducing raw material costs. When using nitrile rubber to reduce the production cost of white and light colored rubber products, it is recommended to use white reinforcing fillers. White carbon black has the best reinforcing effect in the rubber material, and hard clay, active magnesium oxide, calcium silicate, or activated calcium carbonate also have a certain reinforcing effect. Today, the editor will share with you the application techniques of white carbon black and magnesium oxide in nitrile rubber products.
1. Strengthening effect and application points of white carbon black in nitrile rubber products
(1) Reinforcement effect: White carbon black is a white amorphous fine powder with good electrical insulation, low heat generation, light color, and no pollution. After filling with white carbon black in nitrile rubber, the vulcanized rubber has high tensile strength, high elongation at break, good elasticity, and good heat resistance, achieving high tear resistance.
(2) Mixing points: The particle size of white carbon black is small and in a condensed state, making it difficult to disperse in nitrile rubber and nitrile regeneration rubber, which affects the reinforcing effect of white carbon black; In addition, during the mixing of white carbon black, there is a significant increase in heat generation. The Mooney viscosity of the rubber 2SLYY428 filled with white carbon black significantly increases, making the rubber tend to harden. Therefore, an appropriate amount of plasticizer must be added. During the mixing process, increase the mixing temperature appropriately, control the feeding sequence reasonably, improve the dispersion effect of white carbon black, and improve the coke burning performance and strength.
(3) Sulfurization effect: During the manufacturing process of white carbon black, when particles of white carbon black are rapidly generated, the remaining acid inside the particle structure or on the surface makes the white carbon black acidic and does not have a delayed effect on vulcanization; Therefore, when using white carbon black for reinforcement in nitrile rubber products, it is recommended to use alkaline substances such as trihydroxyethylamine for adjustment.
2. Strengthening effect and application points of magnesium oxide in nitrile rubber products
(1) Main uses: Magnesium oxide can be divided into light and heavy types. Light magnesium oxide is a commonly used filler and reinforcing agent in rubber product processes, and can be used as a reinforcing agent for heat-resistant rubber materials in nitrile rubber and nitrile rubber; For example, nitrile rubber with 100 parts of magnesium oxide can withstand heat at 177 ℃. Magnesium oxide can also be used as a sulfurization activator and inorganic accelerator.
(2) Reinforcement effect: Using high-purity calcined magnesium oxide as a reinforcement agent can effectively improve the heat resistance, oil resistance, and bending flexibility of nitrile rubber vulcanizate, with a dosage of up to 100 parts. It should be noted that excessive amount of magnesium oxide in nitrile rubber can increase the compression deformation of the vulcanizate, especially active magnesium oxide; Elongation and cracking resistance decrease.
The influence of active magnesium oxide and ordinary magnesium oxide on the processing performance and Mooney viscosity of nitrile rubber is greatly different. The processing performance of activated magnesium oxide process is poor, and the Mooney viscosity is high; The vulcanizate filled with active magnesium oxide exhibits significant compression deformation, but has excellent heat aging resistance.
When producing rubber products using recycled nitrile rubber as the main raw material, the rational use of thermosetting phenolic resin, polyvinyl chloride resin, polyamide resin, or polystyrene resin as reinforcement materials can also endow nitrile vulcanizate with good heat aging resistance, improve tensile strength, tear strength, and hardness, and improve oil and odor oxidation resistance. In the future, the editor will continue to share with you the varieties and application techniques of commonly used reinforcing agents and fillers for nitrile recycled rubber.
Exclusive original article [commercial authorization] reprint, excerpt and excerpt in any form are prohibited without written authorization. Focus on Hongyun rubber: learn the process formula and raw material technology of producing rubber products from recycled rubber to help you reduce costs and increase profits