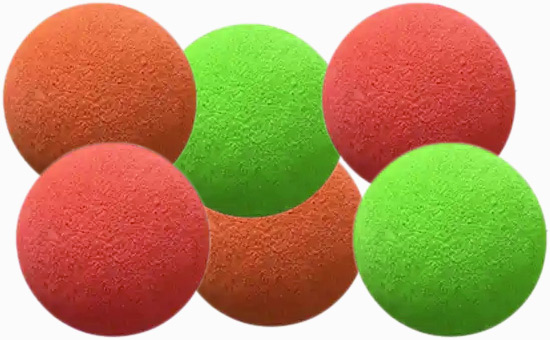
Natural latex recycled rubber has high strength, good elasticity and low price, and is widely used to replace natural rubber to produce various rubber products, effectively reducing the cost of raw materials, foamed rubber products (such as foamed rubber sheets, foam hoses, foam soles, etc.) is one of the categories. When using latex reclaimed rubber to produce foamed rubber products, the selection of reinforcing agents and fillers in the formula is very important; So how to design the reinforcing filling system of latex reclaimed rubber foaming formula?
1. The role of rubber reinforcing agent filler in rubber products
Reinforcing filler is an indispensable part of rubber formulation, and its main role is to improve the mechanical strength, wear resistance, aging resistance, etc. of rubber products. Common reinforcing fillers include carbon black, silica, clay, calcium carbonate, E4LYY57. Carbon black has excellent reinforcing properties, which can significantly improve the tensile strength and wear resistance of rubber; Silica excels at improving the slip resistance and resilience of rubber. In addition, fillers such as clay and calcium carbonate are mainly used to reduce costs and give rubber products a certain degree of rigidity.
2. Factors to be considered when choosing reinforcing agents and fillers for latex reclaimed rubber foam products
(1) Density and dispersion
The ideal reinforcing filler should have a small density and good dispersion, which helps to prevent the hardening of the rubber compound and promote the formation of the hole blank, which is related to the uniformity of the foaming of the product and the surface appearance of the product. In actual production, the dispersed fillers include semi-reinforcing carbon black, easy-to-mix tank black, light calcium carbonate, etc., which can be evenly dispersed in the rubber compound and improve the foaming effect of latex recycled rubber.
(2) The influence of reinforcing agents and fillers on foaming agents
In general, various fillers have little effect on the decomposition temperature and decomposition rate of the blowing agent. The dispersion of the filler is very important for the performance improvement of the rubber sponge, the improvement of the processing performance, the uniform micropore structure and distribution, and the cost.
(3) The balance among the performance and cost of latex reclaimed rubber foamed rubber products
In the foaming formula of latex reclaimed rubber, the selection of appropriate reinforcing filler needs to comprehensively consider the performance requirements and cost control of the product. Too much filler may result in a decrease in flexibility and elasticity of the compound, while too little will not achieve the desired reinforcement.
For example, in the production of sponge foam flooring, clay is usually selected as a filler, and the dosage can be controlled among 30 and 50 parts. Clay can not only reduce the cost of formulation, but also improve the process performance and mechanical strength of the compound. In addition, in order to improve the elasticity and flexibility of the rubber compound, light calcium carbonate can be added in an appropriate amount.
(4) The synergistic effect of reinforcing agents and fillers
In the foaming formulation of latex reclaimed rubber, the synergistic effect of a variety of reinforcing fillers can further optimize the performance of the product.
In the production of latex recycled rubber foam balls, calcium carbonate and clay are usually used together, and a small amount of light calcium carbonate is used at the same time to achieve the dual effect of reinforcement and filling. In addition, by adding the right amount of naphthenic oil, the processability and flexibility of the compound can be improved.
The use of latex reclaimed rubber for the production of sponge foam soles is recommended to use a combination of high styrene and terracotta. The amount of high styrene can be controlled at 10-25 parts, while the amount of clay is adjusted according to the density and strength requirements of the product. The combination of high styrene and clay can effectively reduce costs while ensuring the elasticity and abrasion resistance of latex reclaimed rubber foam soles.
The selection of reinforcing filler in the latex reclaimed rubber foaming formula has an important impact on the performance and cost of the product, and the appropriate adjustment of the variety and dosage of reinforcing agent and filler in the latex reclaimed rubber foaming formula can effectively improve the performance of the foamed product, reduce the production cost, meet the performance requirements of rubber products in different application scenarios, and provide strong support for the market competition of rubber products.
Exclusive original article [commercial authorization] reprint, excerpt and excerpt in any form are prohibited without written authorization. Focus on Hongyun rubber: learn the process formula and raw material technology of producing rubber products from recycled rubber to help you reduce costs and increase profits