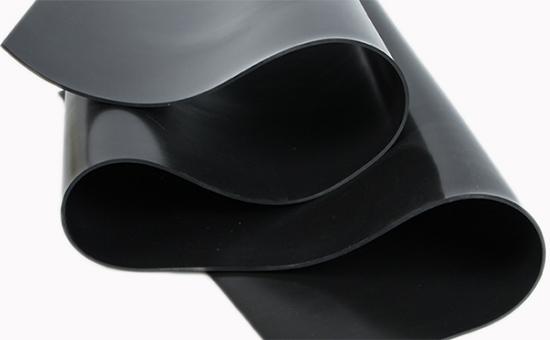
Rubber sheet is a plate processed from rubber as the main raw material, which can be divided into ordinary rubber sheet, acid and alkali resistant rubber sheet, oil-resistant rubber sheet, conductive rubber sheet, etc. according to the use performance. As a recycled rubber resource for the recycling of waste tires, tire reclaimed rubber has a wide source of raw materials and low product prices, and can be combined with other rubber to produce special rubber sheets, effectively reducing the cost of raw materials.
1. Acid and alkali resistant rubber sheet mixed with tire reclaimed rubber vulcanization formula and optimization points
Natural rubber has good alkali resistance and is an ideal raw material for the production of acid and alkali resistant rubber sheets. The use of tire reclaimed rubber can improve cost-effectiveness while maintaining the performance of the rubber sheet. When natural rubber/tire reclaimed rubber produces acid and alkali resistant rubber sheets, sulfur vulcanization is generally selected; The reinforcing filling system can be combined with chemically inert fillers, such as clay, barium sulfate, etc., to further improve the chemical resistance of the rubber sheet; Choose the right antioxidant to further improve the aging resistance of the rubber sheet.
100 parts of natural rubber, 100 parts of tire reclaimed rubber, 7 parts of zinc oxide, 2.5 parts of stearic acid, 1 part of antioxidant D, 5 parts of paraffin, 40 parts of carbon black N330, 232.2 parts of barite powder, 8 parts of black ointment, 0.5 parts of accelerator D, 0.7 parts of accelerator M, 0.1 part of accelerator TMTD, 3 parts of sulfur; Total: 500 copies.
2. Oil-resistant rubber sheet mixed with tire reclaimed rubber vulcanization formula and optimization points
Nitrile rubber is the main raw material of oil-resistant rubber sheet due to its excellent oil resistance; The use of tire reclaimed rubber can optimize costs without compromising the oil resistance of the rubber sheet. When using nitrile rubber/tire reclaimed rubber to produce oil-resistant rubber sheets, sulfur-accelerator system vulcanization is selected; Reinforcing fillers such as carbon black, clay, calcium carbonate, calcium silicate, etc., help to improve the physical properties of the rubber sheet; Use softeners and plasticizers that are not pumped out by the oil, such as low-molecular-weight polyethylene and ointments, to maintain the oil resistance of the rubber sheet.
100 parts of nitrile rubber, 50 parts of tire reclaimed rubber, 5 parts of zinc oxide, 1 part of antioxidant D, 100 parts of carbon black N774, 35 parts of clay, 35 parts of dibutyl phthalate, 0.3 parts of accelerator D, 1 part of accelerator M, 2.5 parts of sulfur; Total: 329.8 copies.
3. Conductive rubber sheet mixed with tire reclaimed rubber vulcanization formula and optimization points
Nitrile rubber is a typical polar rubber and is often used to produce conductive rubber sheets. Tire reclaimed rubber can be used in combination with nitrile rubber in the right ratio to produce conductive rubber sheets, which can reduce costs while maintaining electrical conductivity. When nitrile rubber/tire reclaimed rubber is used together to produce conductive rubber sheets, ordinary sulfur vulcanization systems can also be used; The choice of filler is crucial for conductive properties, and high-structure carbon black such as acetylene carbon black is a commonly used conductive filler; The appropriate use of metal powder can further improve the conductivity of the compound.
100 parts of nitrile rubber, 100 parts of tire reclaimed rubber, 5 parts of zinc oxide, 1.5 parts of stearic acid, 1.5 parts of antioxidant D, 60 parts of acetylene carbon black, 30 parts of calcium carbonate, 30 parts of clay, 25 parts of super wear-resistant carbon black, 25 parts of dibutyl phthalate, 1.8 parts of accelerator DM, 0.5 parts of accelerator CZ, 2 parts of sulfur; total: 382.3 shares.
When special rubber sheets are mixed with tire reclaimed rubber to reduce costs, rubber product manufacturers must reasonably design formulas to ensure the compatibility of reclaimed rubber with other raw materials; Strictly control the production process parameters, such as temperature, pressure and vulcanization time, to ensure product quality; Perform the necessary performance tests to ensure that the rubber sheet meets the specific application requirements; Tire reclaimed rubber is effectively used to produce rubber sheet products with excellent performance and high cost-effectiveness.
Exclusive original article [commercial authorization] reprint, excerpt and excerpt in any form are prohibited without written authorization. Focus on Hongyun rubber: learn the process formula and raw material technology of producing rubber products from recycled rubber to help you reduce costs and increase profits