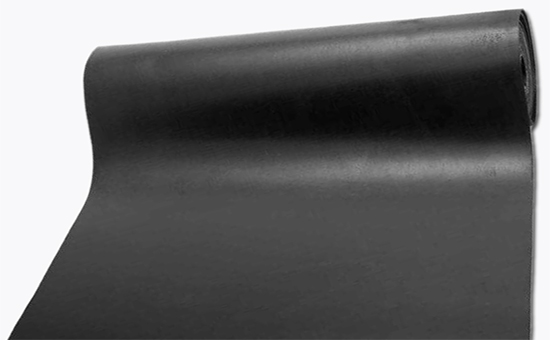
Acid and alkali resistant rubber sheets are mainly used in dilute acid, dilute alkali solution or strong acid, strong alkali and other environments, and the acid and alkali resistance of the rubber compound used is strictly required. Diene rubber has a certain resistance to ordinary acid and alkali, and can be used to prepare ordinary acid and alkali-resistant rubber sheets. When natural rubber is used as the main raw material to produce acid and alkali resistant rubber sheets, appropriate use of tire tread reclaimed rubber can effectively reduce the cost of raw materials; rational design of natural rubber/tread reclaimed rubber acid and alkali resistant rubber sheet formulations can reduce costs while further Optimize finished product quality, improve performance and extend life.
1. Properly increase the amount of sulfur in the natural rubber/reclaimed rubber formula to increase the vulcanization crosslinking density
During the vulcanization process of the rubber material, the crosslinking effect of the rubber compound will increase the density of the rubber compound, so that the active groups and double bonds in the rubber macromolecular structure will gradually decrease; in addition, due to the formation of a network structure, the rubber 2ELYY223 The movement of the chain segment is weakened, and the diffusion of low-molecular-weight substances is seriously hindered, thereby improving the stability of the rubber against chemical substances, and its solvent resistance and heat resistance are also improved. Therefore, increasing the degree of vulcanization and increasing the crosslinking density are effective means to improve the chemical resistance of the vulcanizate.
When natural rubber/tread reclaimed rubber is used as raw material to produce acid and alkali-resistant rubber sheets, appropriately increasing the crosslinking density of the rubber can effectively improve the corrosion resistance of the rubber sheets. When the acid and alkali resistant rubber sheet is vulcanized with sulfur, the amount of sulfur should be increased as much as possible under the conditions of hardness and other physical properties (mostly 4-5 parts), the crosslinking density of the vulcanizate is significantly improved, and the acid and alkali resistance of the finished rubber sheet is better. Okay. In actual production, it is recommended to use accelerator D, accelerator M, accelerator TMTD, etc. for the sulfur vulcanization system. When natural rubber/recycled rubber is used to prepare hard rubber anti-corrosion lining, the amount of sulfur can reach more than 50 parts.
2. The natural rubber/reclaimed rubber combined rubber formula uses inert rubber filler to avoid acid and alkali corrosion
It is recommended to use chemically inert rubber fillers such as clay, barium sulfate, talc, and diatomaceous earth in the formulation of natural rubber/tread reclaimed rubber for acid and alkali resistant rubber sheets; avoid the use of water-soluble fillers and fillers with high water content, and can be used when necessary. Combine with mineral ointment or quicklime to absorb moisture. In acid-resistant rubber sheets, it is not recommended to use substances such as calcium carbonate and magnesium carbonate with poor acid resistance; in alkali-resistant natural rubber/tread reclaimed rubber sheets, silica fillers, phenol resins, talc powder, etc. Corroded rubber packing should not be used.
3. The combination of natural rubber/reclaimed rubber is used to avoid softening plasticizers that react with acid and alkali.
In the formula of acid and alkali-resistant rubber sheet produced by natural rubber/tread reclaimed rubber, softeners and plasticizers that do not act with acid and alkali should be selected. It is recommended to choose low-molecular-weight polymers or alkali-resistant ointments. Esters and vegetable oils are prone to saponification in lye solution, and are often drawn out in hot alkali solution, resulting in product volume shrinkage and loss of working ability. Therefore, ester plasticizers and vegetable oils should be avoided in alkali-resistant plywood. use.
When designing the formula of natural rubber/tread reclaimed rubber acid and alkali resistant rubber sheet, rubber product manufacturers also need to use an anti-aging agent that will not be extracted by chemicals and not easily reacted with chemicals, and add 1-2 parts of paraffin if necessary. A protective film is formed on the rubber surface to avoid direct contact among the acid and alkali medium and the rubber surface, and to a certain extent, the acid and alkali resistance of the rubber sheet is improved. The natural rubber/tread reclaimed rubber can also be mixed with an appropriate amount of plastics with good chemical stability such as polyvinyl chloride, polyethylene, polypropylene, etc., to improve the acid and alkali resistance of the acid and alkali resistant rubber sheet. Later, the editor will continue to discuss with you the application skills and practical formulas of reclaimed rubber in acid and alkali resistant rubber sheets.
Exclusive original article [commercial authorization] reprint, excerpt and excerpt in any form are prohibited without written authorization. Focus on Hongyun rubber: learn the process formula and raw material technology of producing rubber products from recycled rubber to help you reduce costs and increase profits