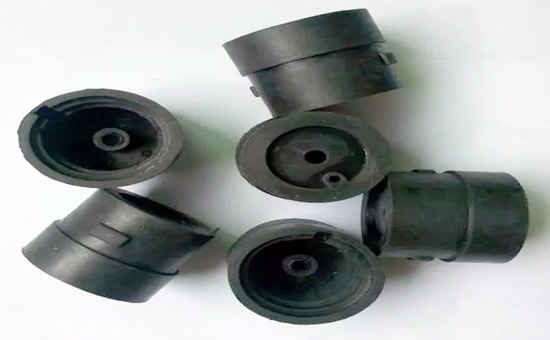
In summer, many extruded rubber products manufacturers will encounter the problem of matte surface or reduced gloss after cooling, if metal products can be surface polished, wear-resistant rubber products how to solve the problem that the surface is not bright enough? First of all, we must analyze the reasons for the lack of luster of rubber products, and solve the problem by prescribing the right medicine. The secret to solving the problem of extruded rubber products surface matte or insufficient gloss after cooling is to solve the problem for the cause, and the loss of light on the rubber surface may be caused by the following reasons:
1. Quality of raw materials: Poor quality of rubber materials or improper selection of additives may lead to unglossy surface of rubber products. The solution is to choose stable and high-quality Hongyun rubber materials and ensure that the quality of additives meets the requirements. The blackness of the surface of rubber products is related to carbon black, softener, glue content, hardness, etc., so we have to analyze the reasons one by one.
2. Process parameters: The setting of process parameters such as temperature, pressure and speed of the extruder head during the extrusion process is unreasonable, which may lead to the surface of rubber products being matte. The solution is to adjust the process parameters of the extruder to suit the characteristics of the rubber material.
3. Formula ratio: the ratio of rubber and auxiliary materials is unreasonable, the most common is light frost or color spraying. Summer temperature high humidity is large, is the rubber products most prone to problems, spring, autumn and winter three seasons of the formula can not be used for summer vulcanization products, the solution is to adjust the summer rubber vulcanization formula of various rubber and auxiliary materials proportion.
4. Post-treatment process: improper subsequent treatment process after extrusion of rubber products (such as insufficient cooling, coating or drying, etc.) may also cause the surface of rubber products to be matte. The solution is to strengthen the control of the post-treatment process to ensure the cleanliness and gloss of the surface of the rubber product. Some rubber products will be coated with silicone oil or Teflon, the surface will be more beautiful, but silicone oil wiping can only temporarily solve the problem, not lasting.
Unreasonable mold design or insufficient mold surface roughness in molded rubber products may also cause the surface of rubber products to be matte. The solution is to optimize the mold design to ensure that the exhaust is smooth, and the inner mold polishing treatment (the coating is prone to sticking to the mold) to ensure that the surface smoothness of the mold meets the requirements.
In addition, high ethylene rubber is selected, the filler is mainly carbon black, and the surface of the rubber product YY23-809 produced is relatively black and smooth; Talcum powder is more suitable for extruding rubber products than light calcium carbonate, and has a certain improvement in surface gloss; Reducing the viscosity of the compound rubber Mooney can also improve the surface brightness of extruded rubber products; If the rubber is not collected, the use of high flash point paraffin oil or high viscosity hydrogenated naphthenic oil will greatly improve the appearance of the extruded product.
The problem of light loss on the surface of extruded rubber products in summer may be caused by many reasons. Choosing high-quality rubber materials and additives first is key; Secondly, it is also important to adjust the process parameters of the extruder to adapt to the characteristics of the rubber material; In addition, reasonable adjustment of the formula ratio of rubber and auxiliary materials, and strengthening the control of the post-treatment process can improve the surface gloss; Unreasonable mold design or insufficient surface roughness will also affect the surface gloss. The use of high ethylene rubber, filler is mainly carbon black, the use of talcum powder or reduced viscosity of compound Mooney, and the use of high flash paraffin oil or high viscosity hydrogenated naphthenic oil can improve the appearance of extruded rubber products.
Exclusive original article [commercial authorization] reprint, excerpt and excerpt in any form are prohibited without written authorization. Focus on Hongyun rubber: learn the process formula and raw material technology of producing rubber products from recycled rubber to help you reduce costs and increase profits