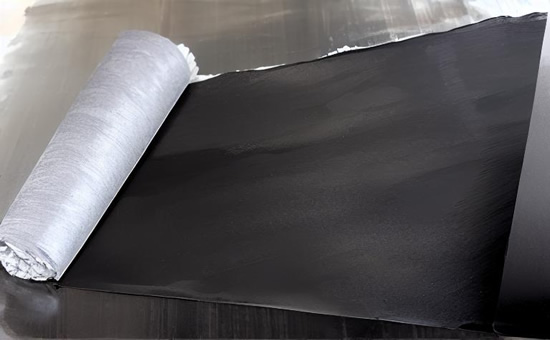
Butyl regenerated rubber selects more than 900 waste butyl inner tubes as the main raw material, after picking the powder, the advanced segmented desulfurization process desulfurization after 80 mesh filtration and refining, with good strength, high fineness, strong air tightness, shock absorption, tasteless, heat resistance, ozone resistance, aging resistance, corrosion resistance, rich hand elasticity and other characteristics, can be used alone or with butyl raw rubber to produce extruded or molded high air tightness products, can also be used with ethylene propylene rubber to improve performance, It is an environmentally friendly material that complies with the EU RoHs 2.0 directive, has similar performance to HY butyl rubber, and is better than butyl rubber in terms of cost performance.
First, the characteristics of butyl reclaimed rubber and the advantages of replacing butyl rubber
Butyl reclaimed rubber is made by recycling waste Y23-725Y butyl rubber and has the following characteristics:
Green environmental protection: the production process of butyl recycled rubber reduces the consumption of natural resources, effectively reduces environmental pollution, and belongs to a new green and recyclable rubber material. Butyl recycled rubber can pass the EU RoHs2.0 environmental protection testing directive.
Stable performance: The physical and chemical properties of butyl recycled rubber are similar to those of butyl rubber, which can meet the requirements of building structure sound insulation pads.
Price advantage: butyl reclaimed rubber production cost is lower, the price is relatively favorable, can provide a higher cost performance.
Second, Hongyun butyl recycled rubber production of building structure sound insulation pad vulcanization formula:
Butyl regenerated gum 100 parts, zinc oxide 3 parts, N550 carbon black 13 parts, stearic acid 2 parts, light calcium carbonate 40 parts, engine oil 14 parts, NBC antioxidants 0.5 parts, paraffin wax 1 part, zinc oxide 0.7 parts, TMTD accelerator 1 part, DM accelerator 0.4 parts, sulfur 1.2 parts; total: 176.8 parts. The recommended vulcanization temperature is 145-155 °C, and the vulcanization time is determined according to the thickness, generally in 40 seconds/mm.
Third, butyl regenerated rubber mixing rubber processing process and points to note
Raw material preparation: butyl regenerated rubber, filler, plasticizer, antioxidant, accelerator, vulcanizing agent are prepared according to the formula ratio.
Compound: Butyl regenerated rubber, fillers, plasticizers, antioxidants are added to the mixer or kneader for thorough mixing. Pay attention to control the mixing temperature and time to ensure that the raw materials are fully mixed evenly. Put the evenly mixed rubber into the rubber turning machine or open mill, and add accelerator and vulcanizing agent (if there is no automatic rubber turning function, you can manually punch the triangle bag and cut the knife operation).
Vulcanization processing: The mixed rubber is weighed in strips and put into the vulcanizing machine mold for vulcanization processing. Control the vulcanization temperature and time to vulcanize the compound.
Post-treatment: post-treatment (such as trimming, cleaning, etc.) of vulcanized rubber products to ensure product quality.
Quality inspection: quality inspection of the sound insulation mats produced for building structures to ensure that the products meet the requirements.
Butyl reclaimed rubber has similar properties to butyl rubber and is more affordable, through the right vulcanization formula and fine rubber mixing processing can produce high-quality building acoustic mats. The application of butyl recycled rubber as an environmentally friendly material in the field of building acoustic insulation mats will bring more environmentally friendly and economical solutions to the construction industry.
Exclusive original article [commercial authorization] reprint, excerpt and excerpt in any form are prohibited without written authorization. Focus on Hongyun rubber: learn the process formula and raw material technology of producing rubber products from recycled rubber to help you reduce costs and increase profits