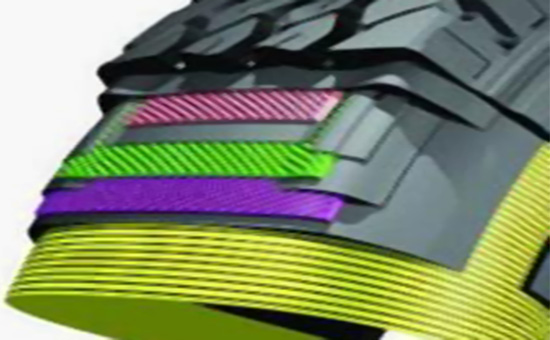
The main function of the inner liner of tubeless tires is to prevent compressed gas leakage, maintain tire pressure, protect the internal skeleton material and rubber layer of tires, avoid them from being eroded by oxygen, ozone and water in the air, and prolong the service life of tires. In actual production, the inner liner of tubeless tires is mostly processed by ordinary butyl rubber and chlorinated butyl rubber with excellent air tightness; The appropriate use of tire reclaimed rubber can achieve multiple functions such as reducing costs, improving the process performance of rubber compounds, and improving the quality of finished products.
1. The inner liner of tubeless tires is mixed with tire reclaimed rubber vulcanization formula
(1) 65 parts of chlorobutyl rubber, 25 parts of natural rubber, 20 parts of tire reclaimed rubber, 5 parts of zinc oxide, 0.5 parts of magnesium oxide, 1 part of stearic acid, 70 parts of carbon black N660, 12.5 parts of naphthenic oil, 4 parts of alkyl phenolic resin, 1.25 parts of accelerator DM, 0.25 parts of accelerator TMTD, 0.7 parts of vulcanizing agent, total: 205.2 parts.
(2) 65 parts of chlorobutyl rubber, 25 parts of natural rubber, 20 parts of tire reclaimed rubber, 5 parts of zinc oxide, 1 part of stearic acid, 40 parts of carbon black N326, 40 parts of clay, 10 parts of paraffin oil, 4 parts of tackifying resin, 1.25 parts of accelerator DM, 0.25 parts of accelerator TMTD, 0.7 parts of vulcanizing agent; Total: 212.2 copies.
2. Key points for the selection of tire reclaimed rubber for tubeless tires
Tubeless tire innerliner films require extremely low air and moisture transmission rates to maintain the pressure in the tire's cavity. When mixing tire reclaimed rubber to reduce the production cost of tire inner liners, it is recommended to choose fine tire reclaimed rubber with a fineness of more than 60 mesh, ultra-fine tire reclaimed rubber E4LYY15, etc., with high fineness, no impurities, and air permeability; In addition, the higher the fineness of the reclaimed rubber, the better the mixing effect with chlorobutyl rubber and natural rubber, to ensure its uniform dispersion in the mixing and extrusion process, and to ensure the uniformity and quality of the inner layer.
3. Tubeless tire innerliner rubber mixed with tire reclaimed rubber formula optimization and process improvement
(1) Formula optimization: when the tire innerliner rubber is mixed with tire reclaimed rubber, the vulcanizing agent VA-7 can be selected, and the accelerator DM and a small amount of TMTD can be used to prolong the scorching time, improve the vulcanization speed and the elongation of the rubber material at break; The use of fast-pressed carbon black can improve the processing technology performance of the rubber compound, increase the tensile stress of the rubber compound, appropriately reduce the elongation at break, hardness and heat generation, and have good thermal conductivity and high temperature resistance.
(2) Process improvement: appropriately increase the mixing capacity during mixing, strictly control the mixing and debinding temperature, and fully preheat the rubber calendering.
When butyl rubber and chlorobutyl rubber produce tire innerliner rubber, you can not only mix tire reclaimed rubber, but also use butyl reclaimed rubber or a small amount of EPDM reclaimed rubber, and continue to discuss related issues with you in the future.
Exclusive original article [commercial authorization] reprint, excerpt and excerpt in any form are prohibited without written authorization. Focus on Hongyun rubber: learn the process formula and raw material technology of producing rubber products from recycled rubber to help you reduce costs and increase profits