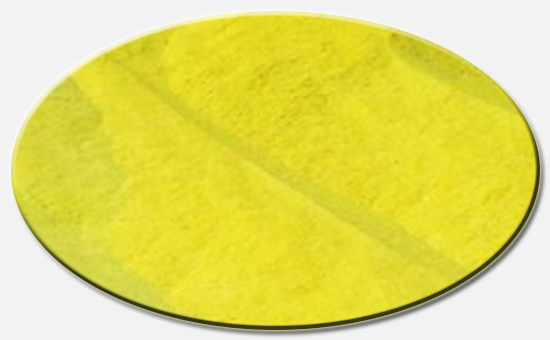
As one of the most widely used types of reclaimed rubber used today, tire reclaimed rubber is also inseparable from the process of vulcanization in production and processing. Rubber vulcanization is a process in which a linear macromolecule is formed by cross-linking a linear polymer, and it can also be said to be a process in which plastic rubber is converted in elastic rubber or hard rubber. The design of the vulcanization system for producing rubber products from tire reclaimed rubber has a great influence on the properties of reclaimed rubber products.
Like all reclaimed rubbers, tire reclaimed rubber can be divided in four stages: vulcanization induction, pre-sulfur, vulcanization, and over-sulfuration:
1. During the vulcanization induction period (scorch-burning time), this process determines the scorchability and processing safety of the tire reclaimed rubber compound. Its length is not only related to the nature of the tire reclaimed rubber itself, but mainly depends on the additives used, such as Longer scorch time can be obtained with a delaying accelerator to achieve higher processing safety.
2. In the pre-vulcanization stage, the low degree of cross-linking in the pre-vulcanization period leads to the tearing strength of the late-stage vulcanizate, and the elasticity cannot reach the expected level, but the tearing and dynamic cracking performance of the tire regenerated rubber compound is better than the corresponding vulcanization. it is good.
3. In the vulcanization stage, the physical properties of the vulcanizates reach or close to the optimum point, respectively, or achieve a comprehensive balance of performance.
4. During the oversulfur stage of the tire reclaimed rubber, the tensile strength continues to increase; for any rubber, not only cross-linking occurs during vulcanization, but also due to the effects of heat and other factors, the breakage of the production chain and the molecular chain occurs. A phenomenon runs through the entire curing process.
When using tire reclaimed rubber to produce rubber products, the design of vulcanization system directly affects the properties of reclaimed rubber. Most of them are sulfur vulcanization systems, among which sulfur, accelerator, zinc oxide and stearic acid affect the physical indicators of tire reclaimed rubber products, with 100 tires. Reclaimed rubber is a standard: When 1.5-2 parts of sulfur is used, the tensile strength and the elongation at break of the reclaimed rubber can reach the maximum; the excessive amount of the accelerator can cause the tensile strength of the reclaimed rubber to decrease greatly, generally 0.5 parts is the best. Can be used in combination; zinc oxide dosage is between 2-3 parts; stearic acid dosage is related to zinc oxide dosage, generally 1-1.5 parts.
The vulcanization process in the production of tire reclaimed rubber products is generally the same. When rubber products are produced from tire reclaimed rubber, the design of the vulcanization system is directly related to the quality of the rubber products. The rubber product manufacturers must strictly design the formula; Hebei Hongyun Reclaimed Rubber Factory has experience Experienced rubber engineers and professional technicians can help you design recycled rubber formulas, optimize formulas, and minimize the cost of rubber products.
Exclusive original article [commercial authorization] reprint, excerpt and excerpt in any form are prohibited without written authorization. Focus on Hongyun rubber: learn the process formula and raw material technology of producing rubber products from recycled rubber to help you reduce costs and increase profits